Industrial companies, especially those with complex technological processes, often face numerous operational and technical risks that can lead to failures, downtime or even accidents. Without proper classification analysis and assessment, we are unable to implement measures to reduce potential risks or their effects.
Hazard analysis<br> and risk assessment
In industry, one of the most common methods for identifying risks is the HAZOP (Hazard and Operability Study), where a multidisciplinary team identifies and categorizes individual hazards, according to a predetermined scenario. The risk analysis is applicable in Industrial Automation, where the primary goal is to identify hazards and assessment of the operational capabilities of the control system. C-HAZOP (Control Hazard and Operability Studies) analysis helps minimize the risk of failure, increase safety and optimize production processes.
The Machinery Directive 2006/42/EC and the REGULATION OF THE EUROPEAN PARLIAMENT AND COUNCIL (EU) 2023/1230 regulation of June 14, 2023, which will take effect from 2027, define risk assessment obligations, vis-à-vis manufacturers of machinery and equipment.
To meet the needs of the market, our company supports manufacturers and end users by performing various types of analysis in the field of risk identification and assessment.
Find out how we can support your business
Insufficient
identification of risks
Without properly performed analysis, identification and classification of risks, it is impossible to build systems to reduce risks.
Downtime and breakdowns
Underestimating the identification and assessment of risks can lead to dangerous situations in which the Employer loses control . Based on our knowledge and experience, we help our clients identify risks.
Operational inefficiencies
Lack of risk analysis and implementation of preventive measures is also a problem in the human area. Employees are reluctant to perform tasks being aware of the surrounding.
Step by Step
Hazard analysis, is a process that involves the detailed identification of hazards and evaluation of the operability of control systems. From the initial analysis to the implementation of recommendations, it aims to improve employee safety. Depending on the characteristics of the plant and the client’s preferences, hazard analysis and risk assessment are performed using the following methods:
PHA (Preliminary Hazard Analysis).
HAZOP (Hazard and Operability Studies) – Hazard and Operability Analysis
C-HAZOP (Control Hazard and Operability Studies) – Automation Hazard and Operability Analysis
LOPA (Layer of Protection Analysis).
FTA (Fault Tree Analysis).
ETA (Event Tree Analysis).
SIL (Safety Integrity Level).
FSA (Functional Safety Assessment)
FMEA (Failure Mode and Effects Analysis)
RBI (Risk Based Inspection) – Inspection Planning Based on Risk Analysis.
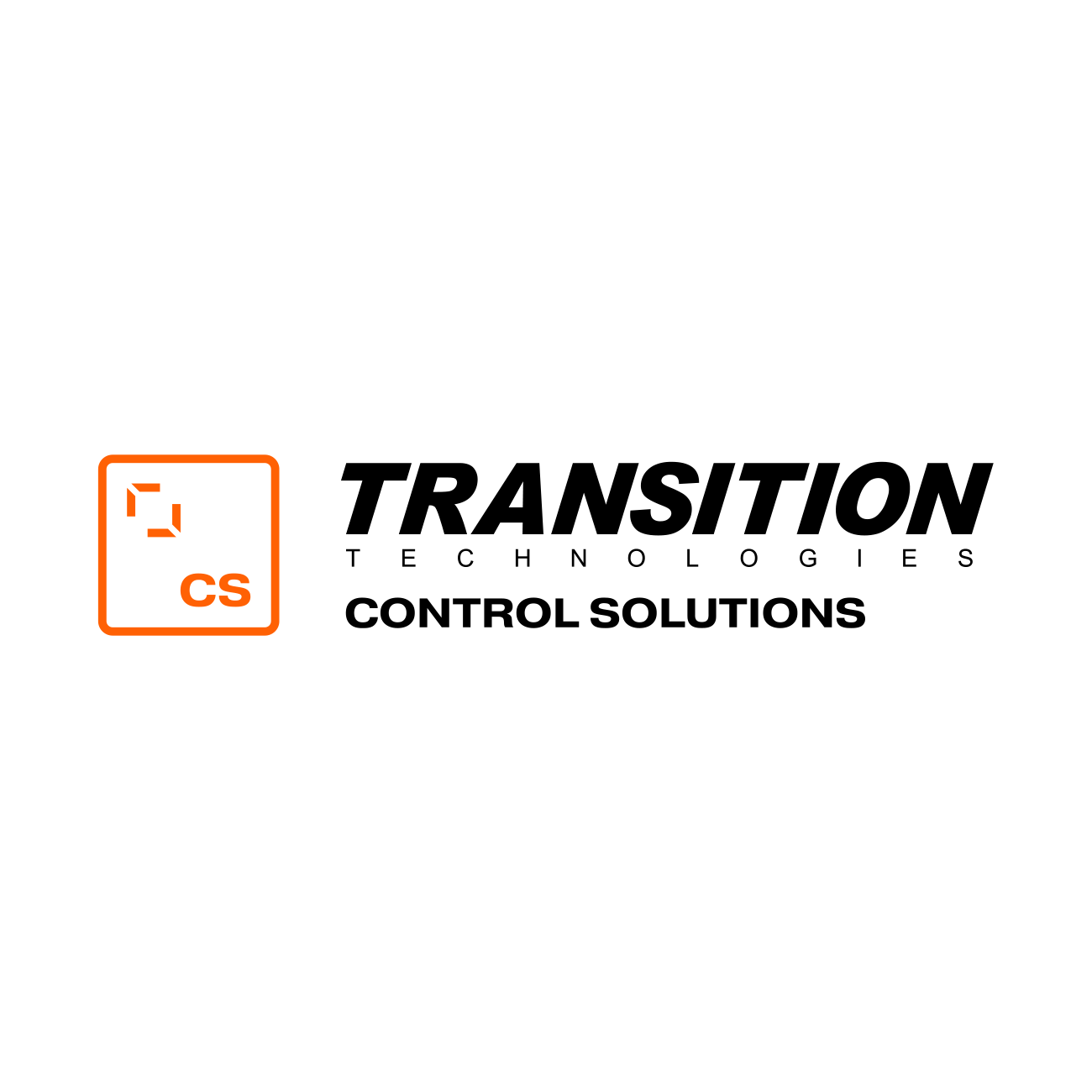
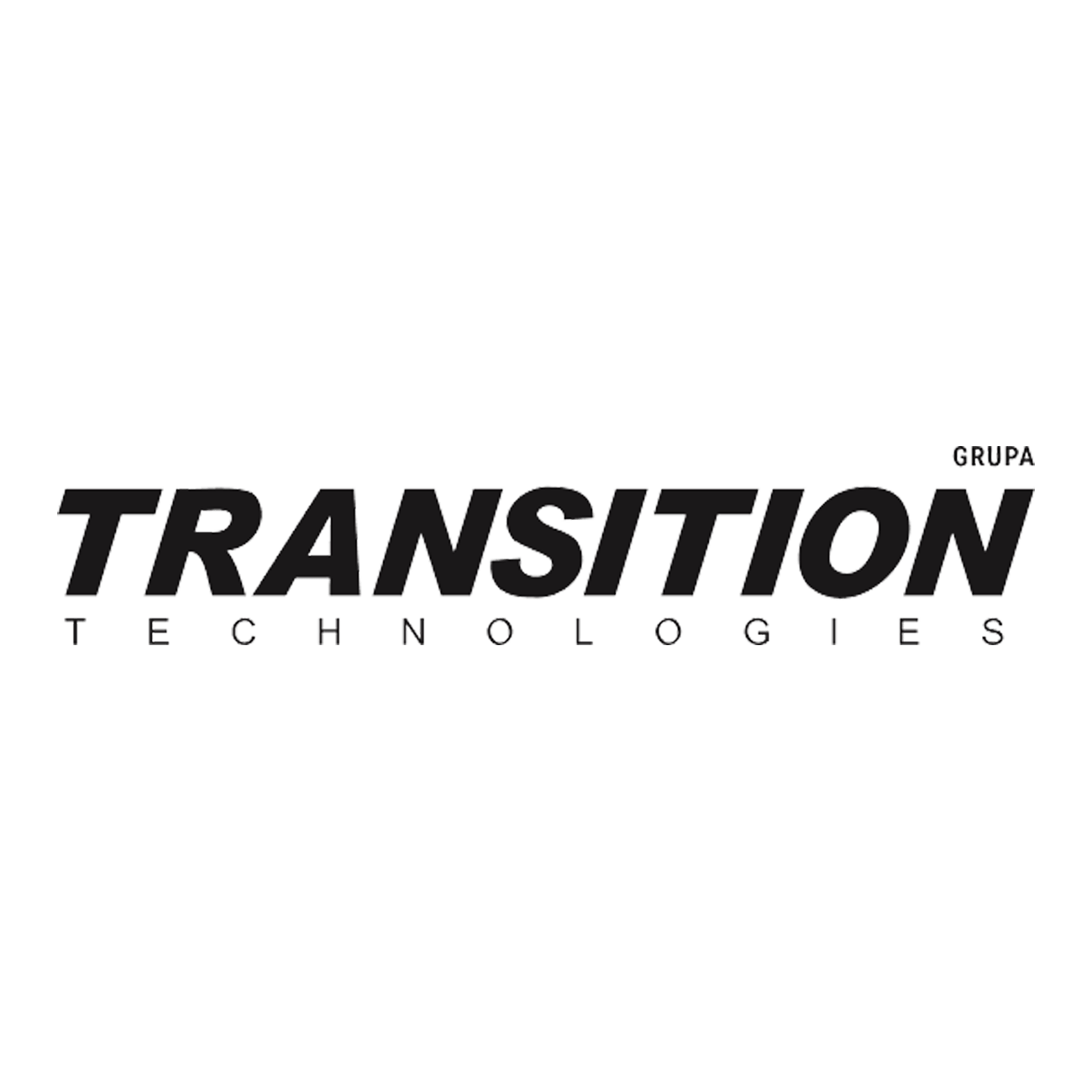
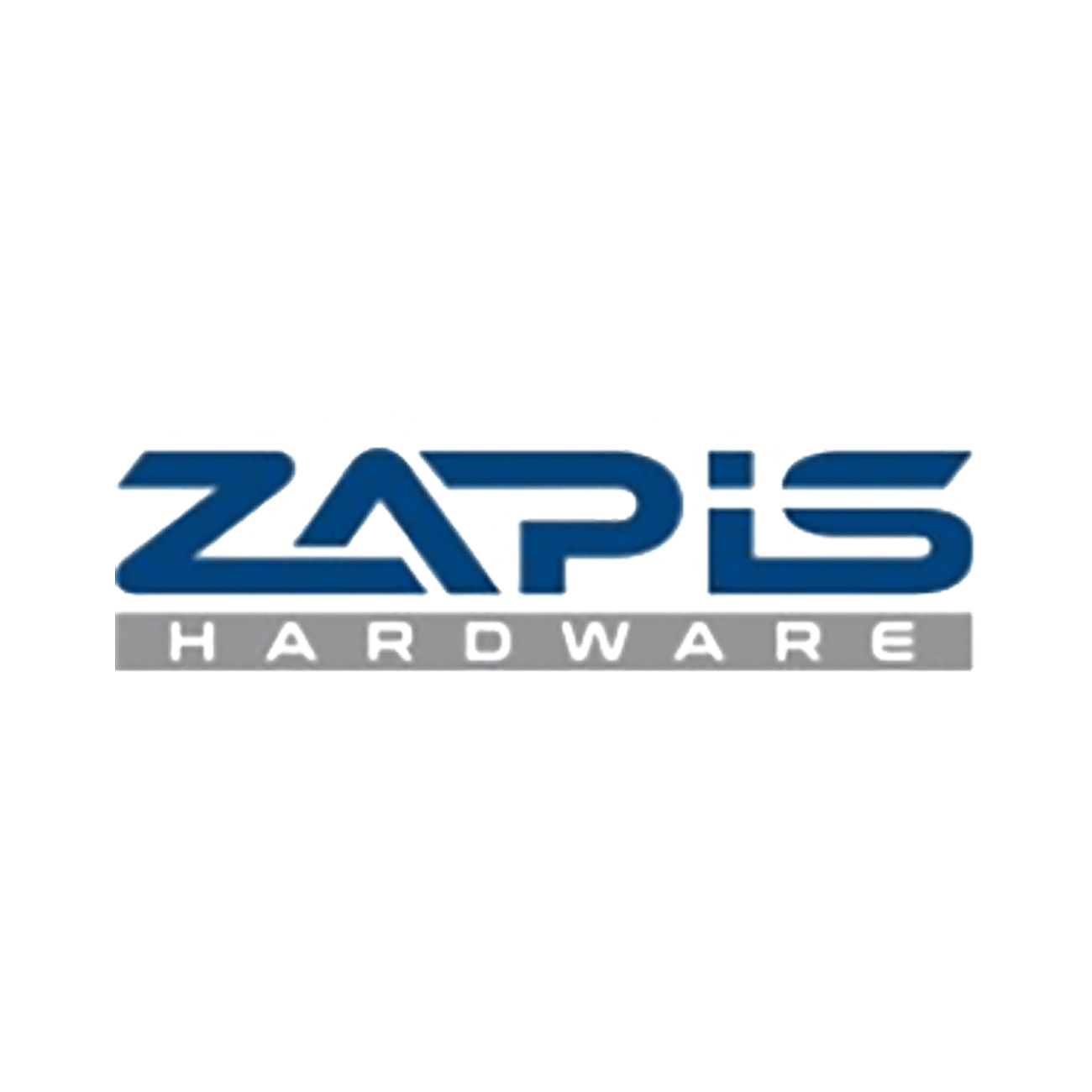
Competitive Advantage
We are part of the renowned Transition Technologies Group, which has been creating the future of industrial technology since 1991. The group includes 21 companies, employs more than 2,280 specialists and operates from 27 offices around the world, operating with 100% Polish capital. Our mission is to provide innovative technology solutions that drive global industry growth.
- Innovation: We constantly invest in the latest technologies to keep our solutions at the forefront of innovation.
- Experience: More than three decades in the industrial technology market provide us with the knowledge and skills needed for the most demanding projects.
- Quality: We are ISO 9001:2015, ISO 27001:2013 and ISO 45001:2018 certified, confirming our commitment to the highest standards of quality and safety.
When you choose our solutions, you are investing in the future of your business – a future that is innovative, efficient and sustainable.
We work with the best:


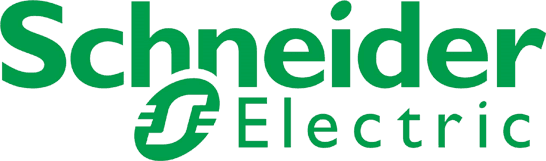
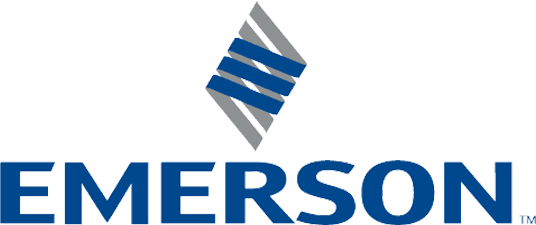

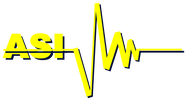
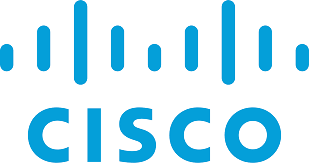
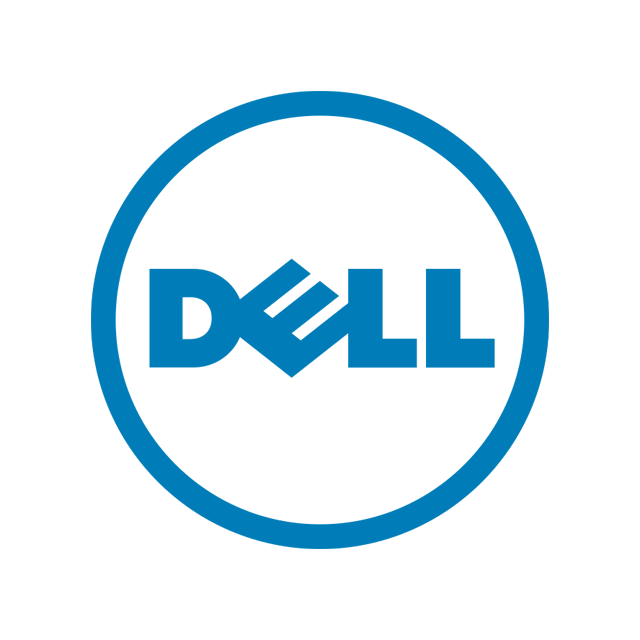
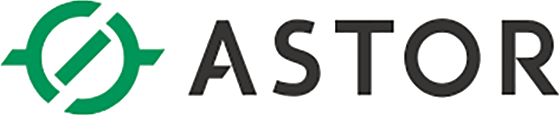
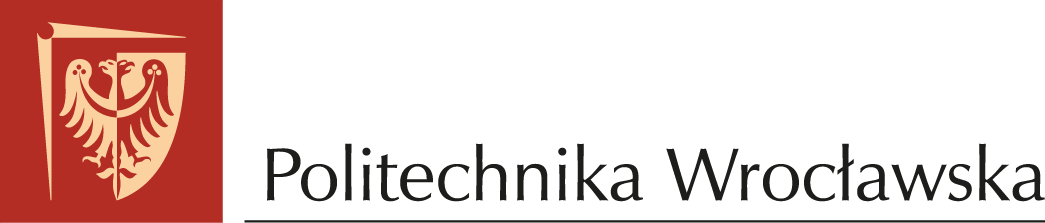
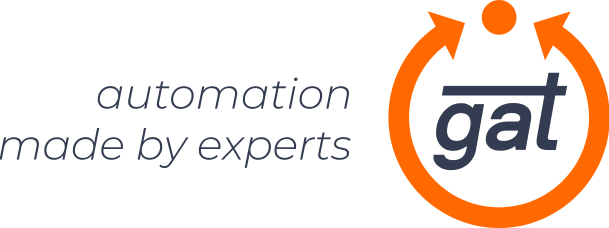
Opinions of Our Customers
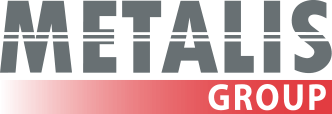
”From the very beginning of our cooperation, Transition Technologies-Control Solutions has made itself known as a reliable partner. What set them apart was their creative approach at the bidding stage. We were presented with several proposals for solutions based on which we could choose a target direction.</p>
Adam BombaProcess Manager
<p>During implementation, on the other hand, they acted with determination, solving successive problems that arose. Faced with the fact that the project was implemented in a difficult market environment, we often had to work together and develop remedies, often through compromise. Also, during the operation of the site, they reacted constructively and quickly to faults as they appeared.</p>
<p>TT-CS has proven itself as a trusted partner in challenging projects. We positively look forward to working together on future mechanical engineering projects.
Our experts guarantee the quality of services
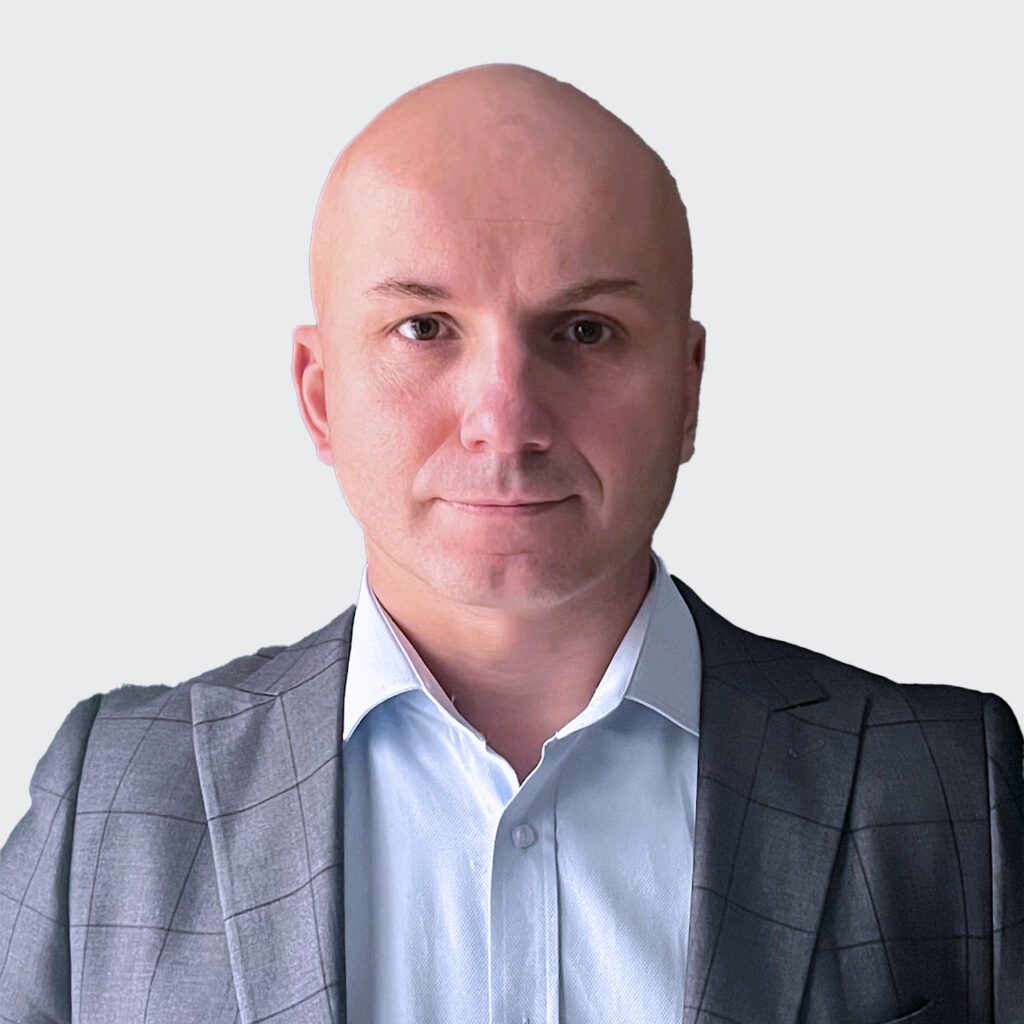
He graduated from the Wroclaw University of Technology, majoring in automation and robotics, and from the University of Wroclaw and Lodz, where he studied Computer Science.
He has been with Transition Technologies Group since 2008, and has actively participated as a solution integrator in many projects around the world, in the field of industrial automation in the energy sector.
Since 2022, he has been the Director of Industrial Automation. strategic projects. He is responsible for the implementation of key projects for the company, mainly in the energy and Gas & Oil sectors at Transition Technologies-Control Solutions.
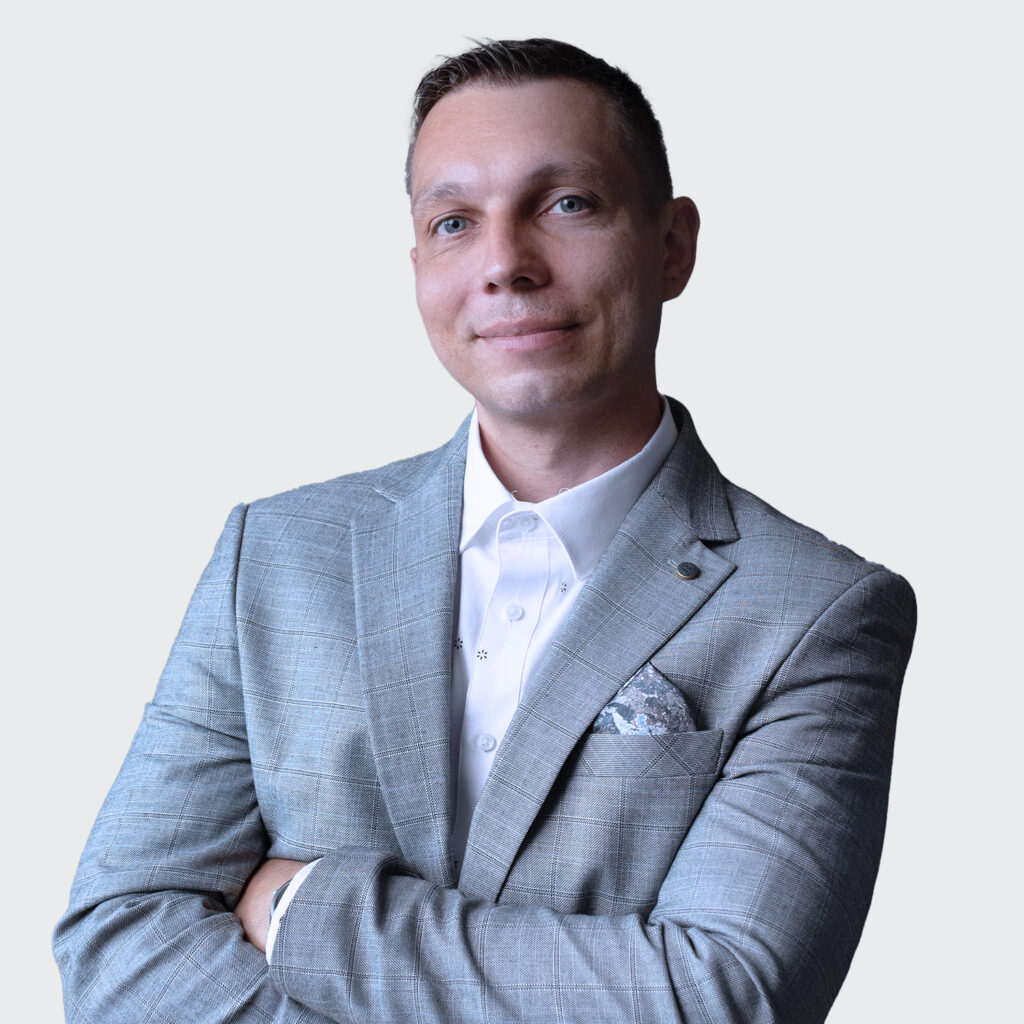
He is a graduate of Wroclaw University of Technology, where he completed his master’s degree in Automation and Robotics at the Faculty of Electronics, and Wroclaw University of Economics, where he completed postgraduate studies in Project Management. He has been an active engineer since 2011, focusing his interests in the area of process automation. He has been with Transition Technologies Group for more than five years, serving as an engineer and designer (instrumentation and control systems).
Since 2022, he has served as Manager in the Strategic Projects Department at Transition Technologies-Control Solutions.
He is a member of PIME. He holds Prince2 certification, which confirms his competence in managing large projects.
Its portfolio boasts a number of projects on strategic facilities and for critical infrastructure, including. leading the ACP work on the construction of Baltic Pipe.
He is currently expanding his knowledge and competence in the area of functional safety and hazard analysis.
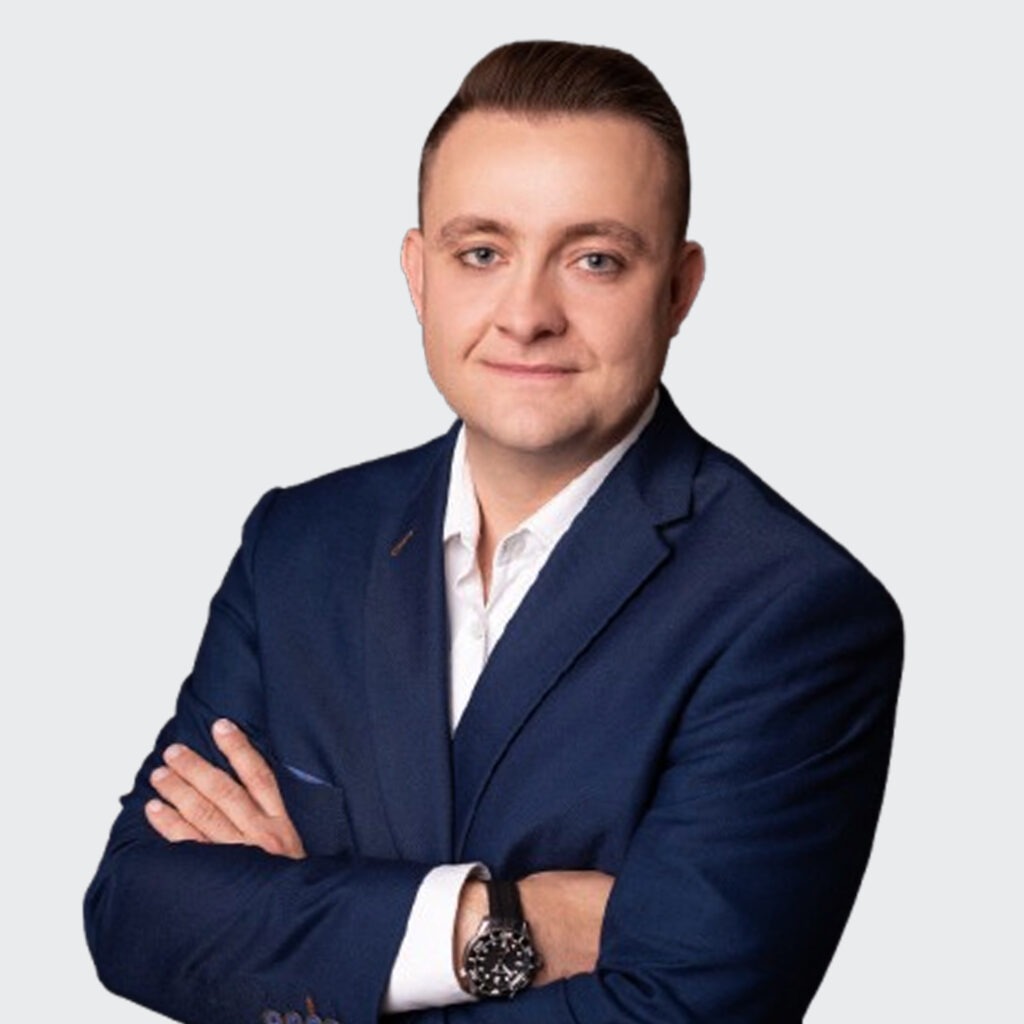
A graduate of Kielce University of Technology, where he majored in Environmental Engineering at the Faculty of Construction and Environmental Engineering. His entire career has been in the technical industry, where he effectively combines engineering knowledge with business and interpersonal skills to support sales processes for technology and engineering solutions.
To grow in the field of industrial automation, he joined the TT-CS team. He is passionate about aquariums and terrariums, creating and nurturing complex ecosystems for aquatic and exotic animals. His hobby requires precision and patience, which is reflected in his professional approach to his work
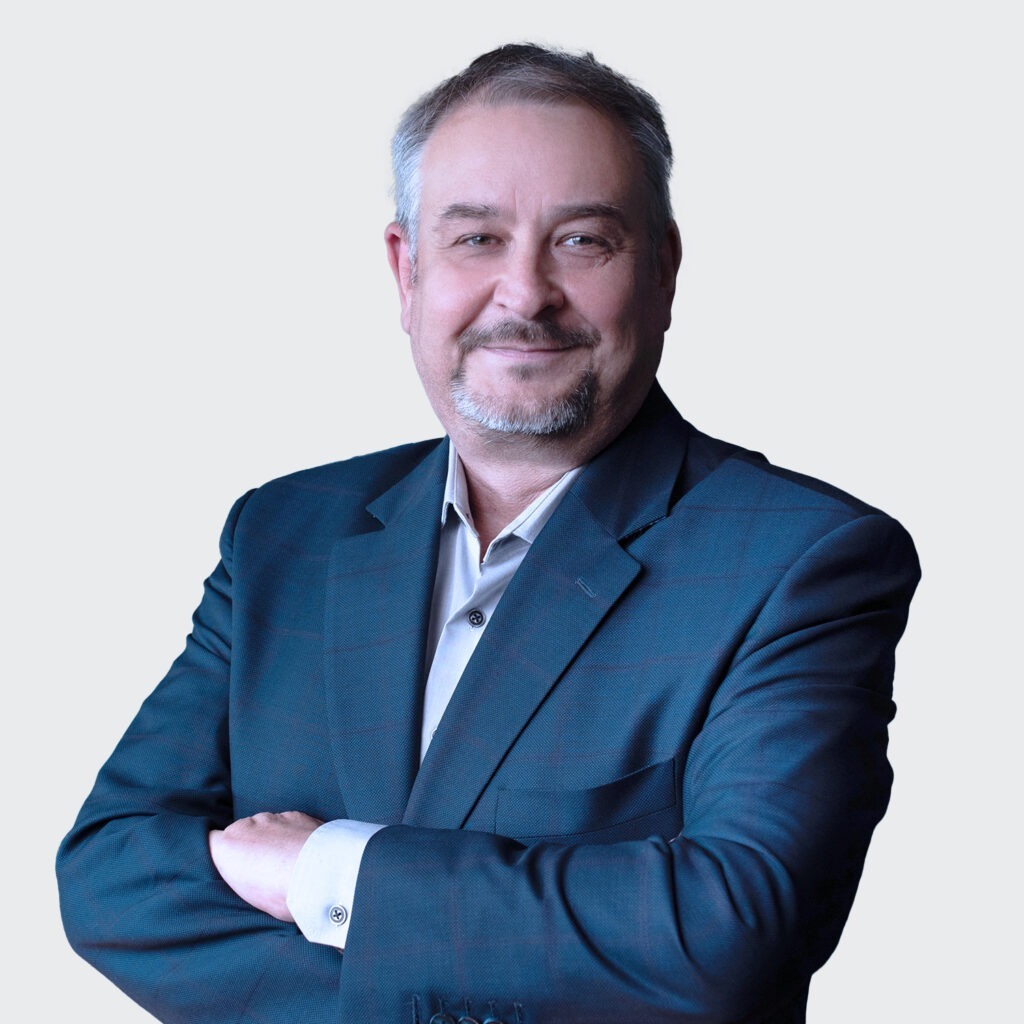
A graduate of Wroclaw University of Technology, where he graduated in 1990 with a degree in Electron Technology from the Department of Electronics. He began his career as an assistant designer at the “Record” Automation Systems Company.
He has been with Transition Technologies Group for more than 26 years.
For more than 12 years, he has served as Project Manager at Transition Technologies-Control Solutions.
In his role, he manages the implementation of industrial automation projects.
We Are Here to Help
Are you interested in our offer?
Write to us for a personalized consultation.
- Individual counseling
- Tailored solutions
- Quick implementation
- Experts with experience
Fill out the form and get a free consultation
Questions
and answers
In the FAQ section, you will find answers to key questions about our services and processes, based on knowledge and experience. Our goal is to dispel doubts and provide clear information.
What is CHAZOP analysis and why is it important for my plant?
CHAZOP (Hazard and Operability Study) analysis is the process of systematically evaluating control systems for potential hazards and operational problems. It is critical to ensuring plant safety and efficiency. It identifies risks associated with equipment failures, system errors or operational problems, minimizing the risk of downtime, accidents and financial losses.
What are the benefits of conducting a CHAZOP analysis?
CHAZOP analysis brings many benefits, such as identifying potential hazards at an early stage so that preventive measures can be taken. It also helps optimize control systems, improve their reliability, and implement better operational and safety procedures. As a result, the plant can operate more efficiently, with less risk of downtime and greater control over processes.
In which industries is CHAZOP analysis most commonly used?
CHAZOP analysis is widely used in industries with high levels of automation and operational complexity, such as the chemical, oil, gas, energy and pharmaceutical industries. In these sectors, production processes require constant control, and minimizing operational risks is crucial for safety and efficiency.
What are the most common problems detected during CHAZOP analysis?
Problems such as inconsistencies in control systems, shortcomings in safety procedures, lack of redundancy in key systems, insufficient process monitoring and lack of adequate emergency preparedness are often detected during CHAZOP analysis. All of these problems can lead to an increased risk of failure and downtime.
What does the CHAZOP analysis process look like?
The CHAZOP analysis process begins with a detailed analysis of control systems and processes. This is followed by workshop sessions involving automation and safety experts and key plant personnel. Together, potential risks and operational irregularities are identified. Based on the results of the analysis, a report with recommendations is developed to help implement corrective and optimization measures.
What action should be taken after a CHAZOP analysis?
Following the CHAZOP analysis, the plant should implement the report’s recommendations. This may include upgrading control systems, improving safety procedures, training personnel and introducing new operating standards. Implementing these measures will minimize the risk of future accidents and optimize plant performance.