Doosan Cobots
- Security and cooperation
- Versatility and flexibility
- Mobility
- Modernity and advanced features
- Ease of use
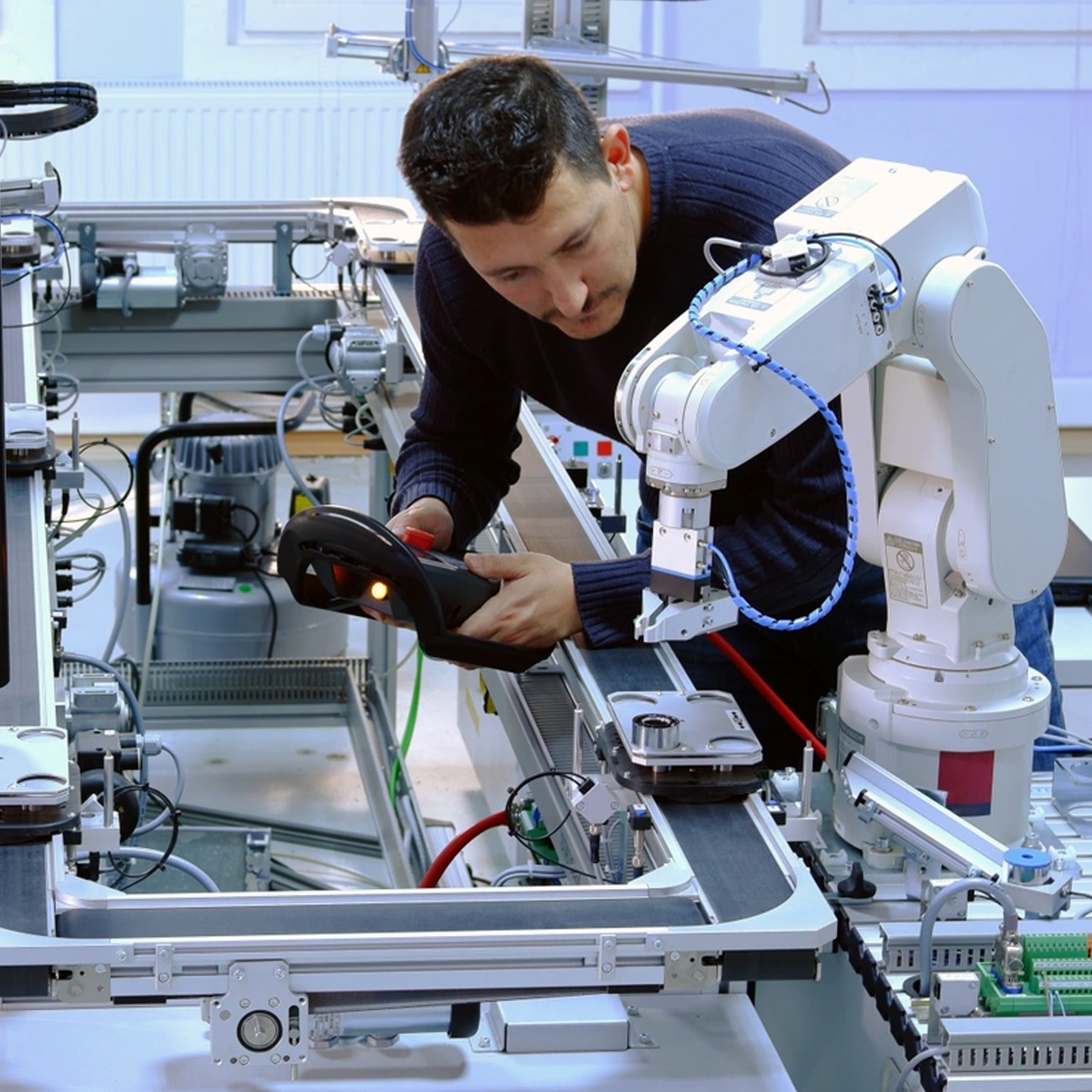
Security and cooperation
One of the most important aspects of Doosan cobots is their ability to work safely with humans in the same workspace. Doosan cobots are designed for maximum safety in operation, eliminating the need to install additional safety barriers.
Main advantages:
- Working side-by-side with the operator.
With advanced force sensors, cobots can work directly with humans, increasing production efficiency. - Sensitive collision detection.
Cobots are equipped with systems that detect even the smallest obstacles, automatically stopping work to avoid collisions. - Programmable safety features.
Cobots meet all the latest safety standards and norms (ISO 10218 and ISO/TS 15066), making them safe even in harsh industrial environments.
Benefits: Improved workplace safety without the need for additional guards, reducing installation costs and occupied workspace.
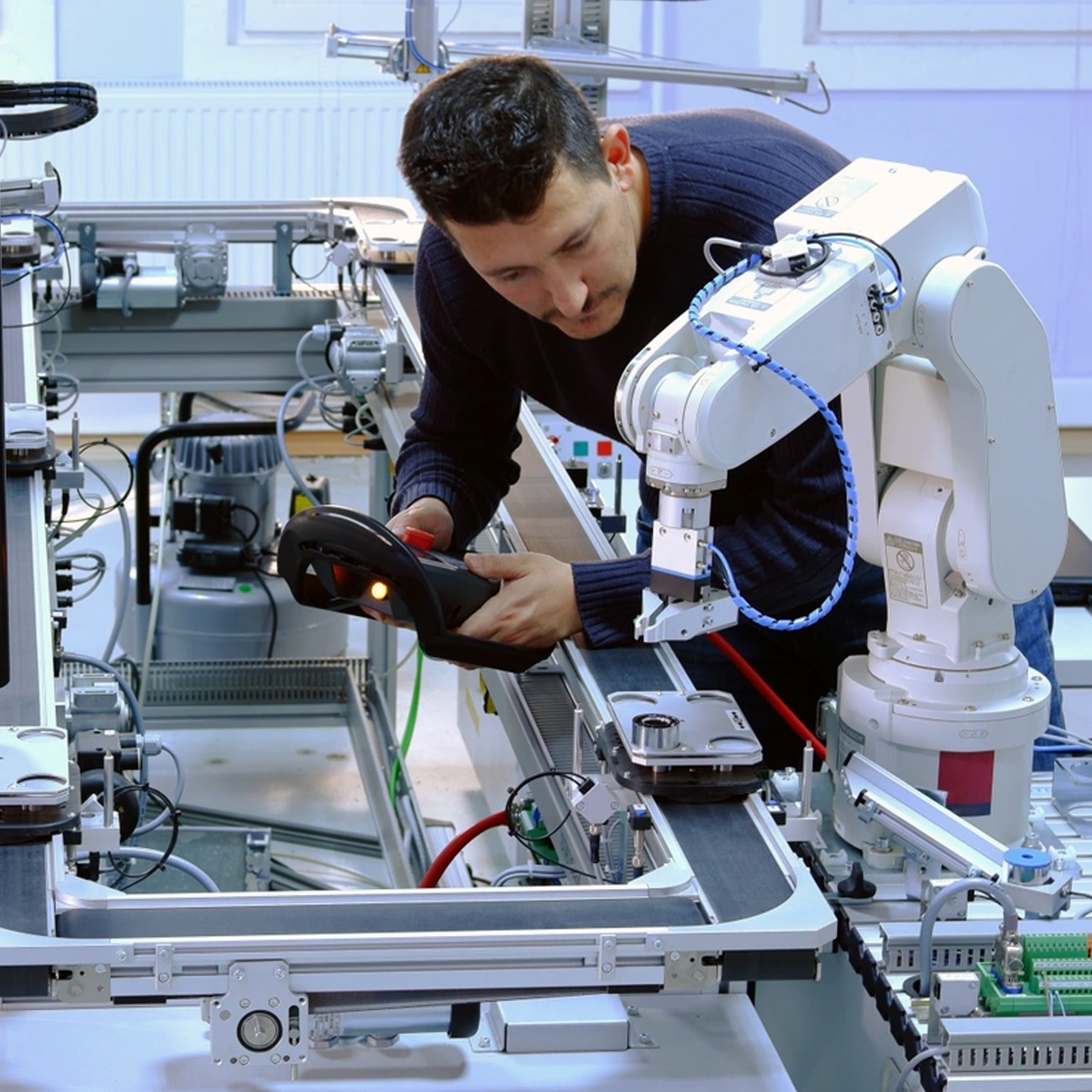
Versatility and flexibility
In today’s changing manufacturing environment, flexibility is key. Doosan Cobots are extremely versatile, allowing them to quickly adapt to new tasks
- Easily adaptable to different tasks.
With a versatile design and standard interfaces, the cobots can be used in a wide variety of applications, from assembly to packaging. - Short development time for new programs.
Even complex production processes can be reprogrammed quickly, speeding up adaptation processes in production with short cycles. - Compact design.
Cobots take up little space, optimizing workspace in the manufacturing plant.
Benefits: Increased production line flexibility and the ability to respond quickly to changes in the production process without prolonged downtime.
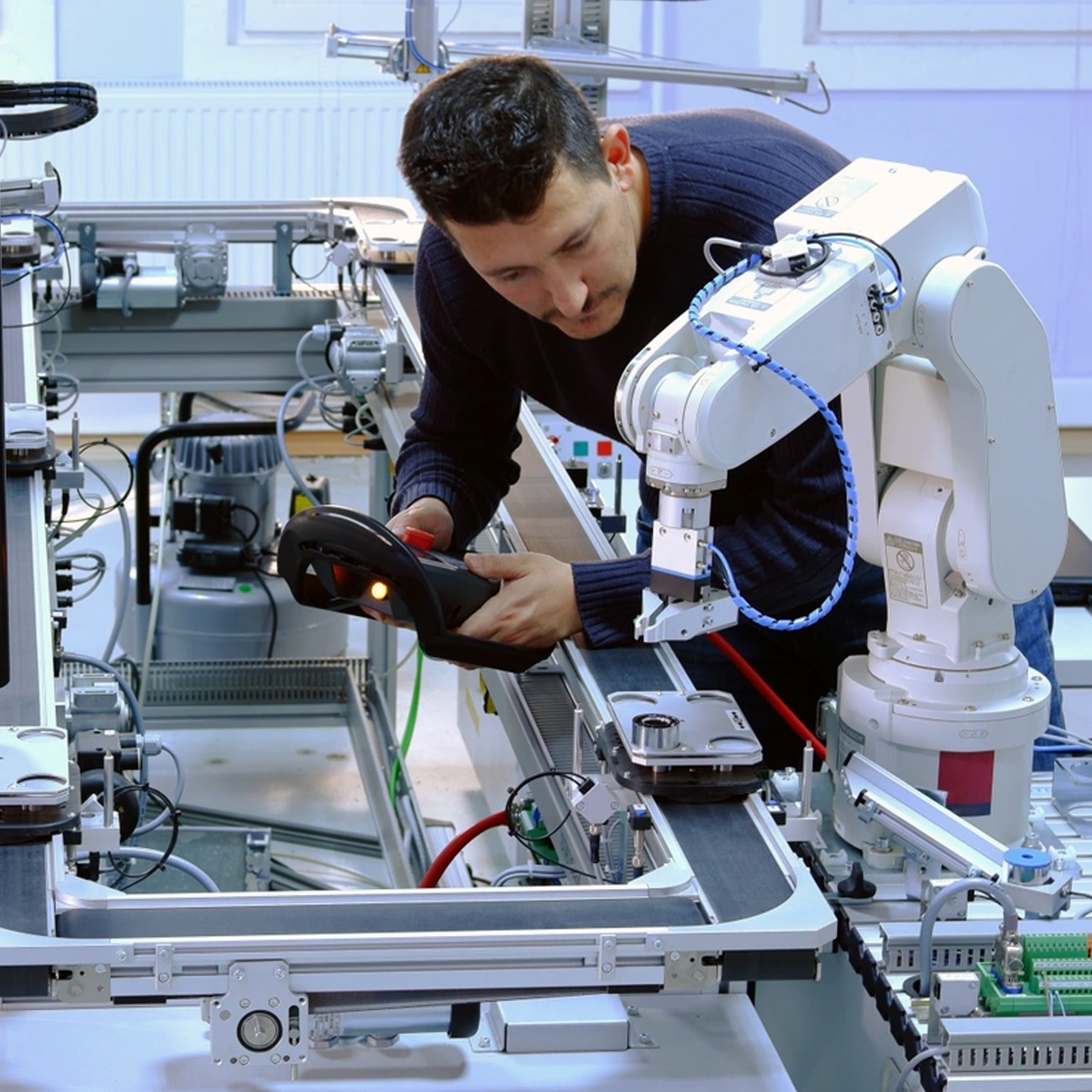
Mobility
Doosan Cobots are distinguished by their lightweight and handy design, which makes them extremely mobile. They can be easily moved between different workstations or mounted on mobile platforms such as AGV (Automated Guided Vehicle) or AMR (Autonomous Mobile Robot).
- Easy transportation.
Thanks to the low weight of cobots, it is possible to quickly move them to new production zones without the need for costly and time-consuming installations. - Mounting on mobile platforms.
Cobots can be mounted on mobile carts to dynamically adapt to changing production needs.
Benefits: Increased flexibility of production lines and ease of moving cobots, allowing for better space management in the plant.
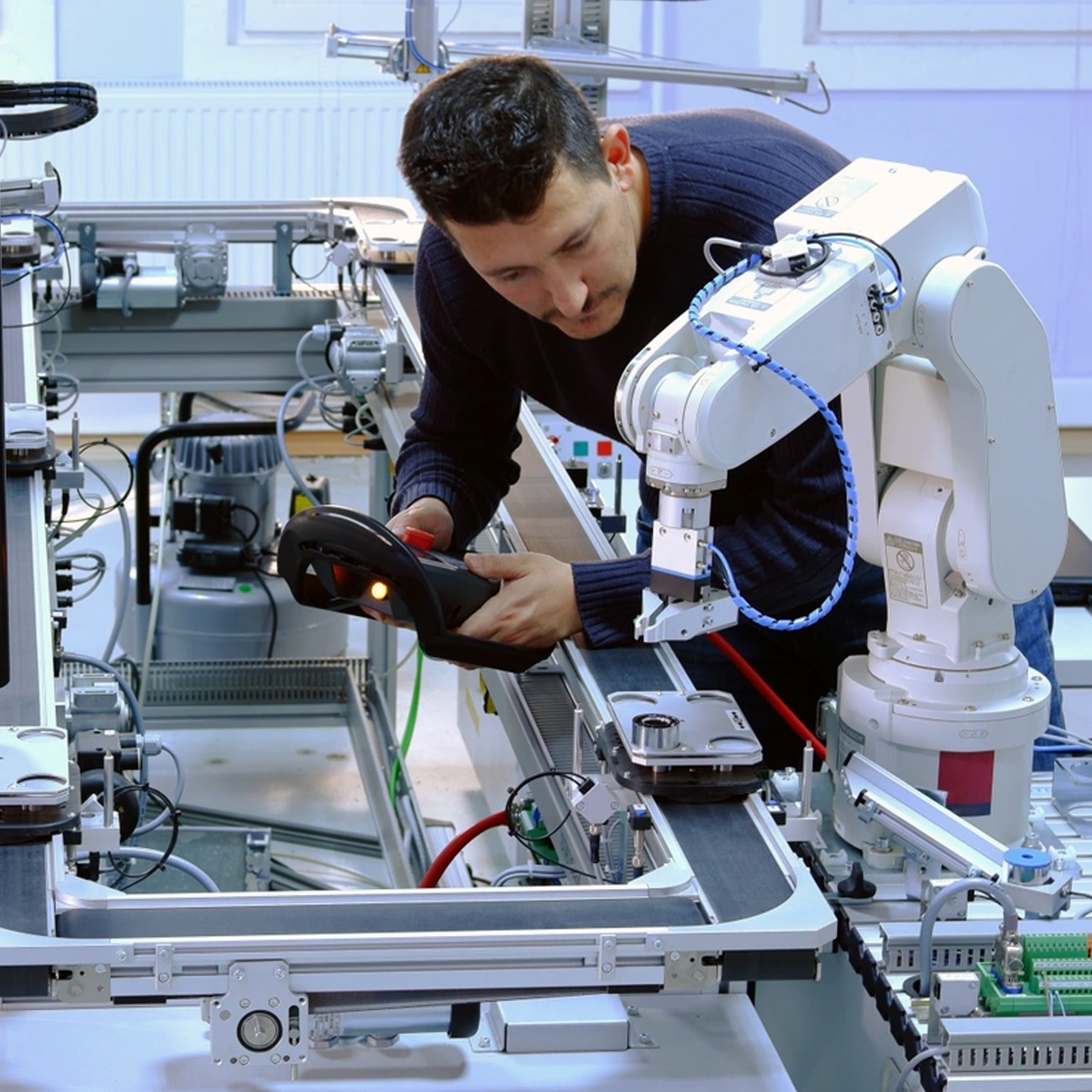
Modernity and advanced features
Doosan Cobots are not only state-of-the-art collaborative robots, but they are also equipped with advanced programming features that enable them to perform even the most complex tasks.
- Force-sensor-based functions.
Force detection and acting with a set force on an object, which is extremely useful in processes such as assembly, grinding or polishing. - Ecosystem DR DART Suite.
A platform that allows users to create their own applications, remotely manage cobots, and share experiences and software with other users. - Ability to use scripts.
Advanced users can create complex programming sequences, customizing cobots to meet specific production needs.
Benefits: Increased programming flexibility and the ability to fully utilize the potential of cobots in modern production environments.
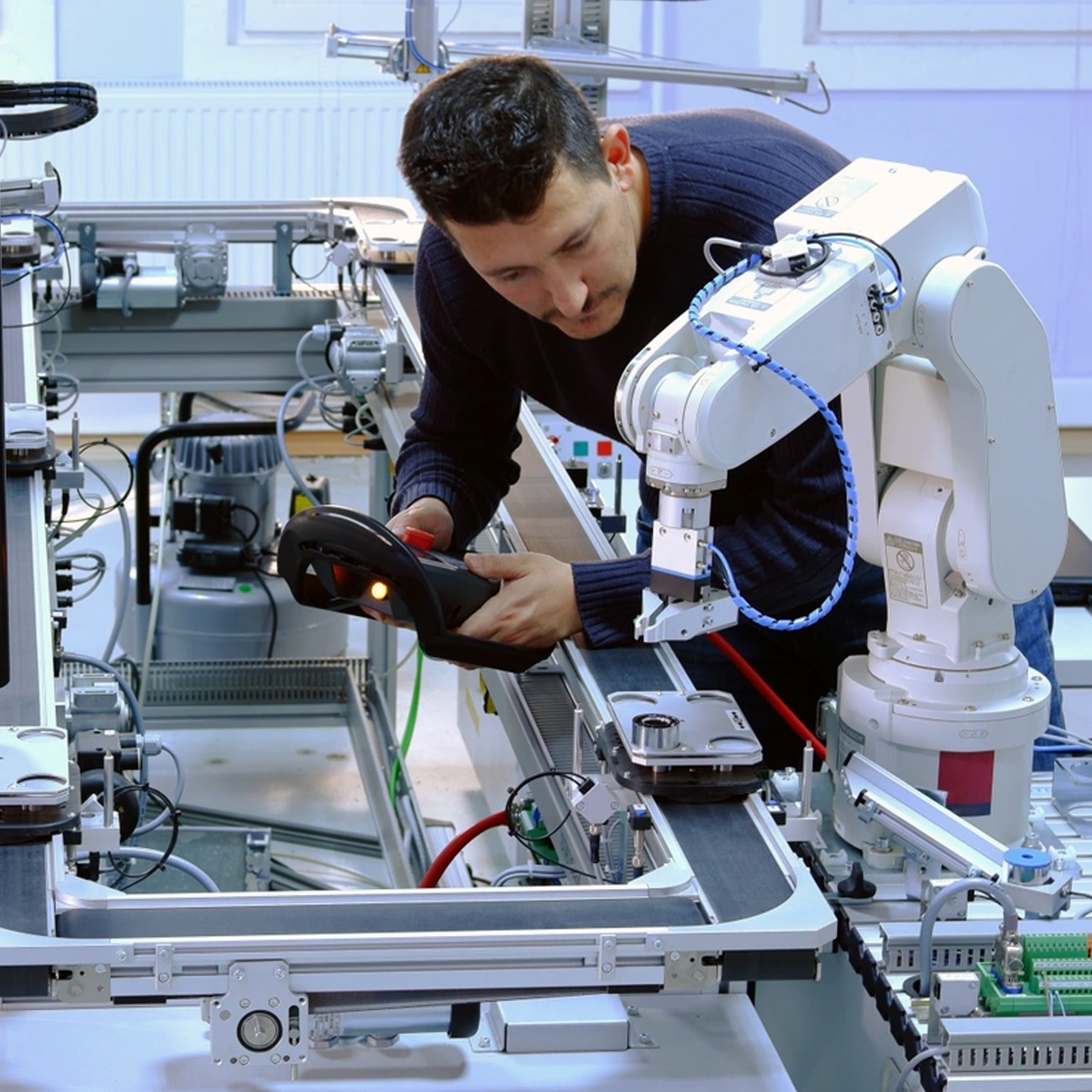
Ease of use
Doosan Cobots are designed for ease of use and programming, making them ideal for both small and medium-sized companies that may face a shortage of skilled engineers.
- Intuitive user interface.
Simple and clear software enables quick and hassle-free programming even for those without robotics experience. - Easy programming.
Doosan Cobots can be programmed by manually guiding the robot to process points, minimizing setup time. - Immediately ready for deployment.
Cobots are ready to work almost immediately after delivery, without the need for complex integration with existing systems.
Benefits: Faster implementation, fewer technical requirements, and the ability for people without robotics experience to program.
Examples of applications
Palletization and depalletization
Doosan Cobots are ideal for palletizing processes, where they precisely stack products on pallets, and for depalletizing processes, where they easily unload them. Thanks to their versatility, they can adapt to different types of products and packaging, providing:
- Optimize logistics processes.
Reduce palletization time, which contributes to increased production efficiency. - Savings.
Lower unit costs due to automation that eliminates the need for manual stacking of products. - Agility.
Easily reconfigure when new product types or pallet stacking patterns are introduced.
Welding
Doosan Cobots can be used in welding processes, providing:
- High precision.
The ability to program accurate welding paths, which guarantees the repeatability and quality of the welds made. - Safety.
Cobots can work alongside operators, eliminating the risk of accidents and reducing the need for enclosure. - Reduced learning time.
Intuitive interface means that even operators with minimal experience can quickly learn to program the cobot for welding.
Screwing
Precision screwing of parts is one task where Doosan cobots excel. Thanks to advanced programming features, they can:
- Automate the assembly process.
Enable faster and more precise screwing compared to manual work. - Adjust pressure.
Which is especially important in the assembly of delicate components such as electronics. - Increase repeatability and quality.
Eliminating errors due to improper tightening or omission of a component.
Pick & Place
Doosan Cobots are ideal for pick & place applications, that is, moving and positioning products to specific locations on the production line. In such tasks they offer:
- Speed and precision.
Ideal for sorting, segregating and placing products in the correct containers. - Flexibility.
Easily adaptable to changing products or production requirements. - Integration with vision systems.
Cobots can work with cameras, allowing them to recognize products and precisely place them in designated areas.
Grinding and polishing
Doosan Cobots can also be used for tasks that require precise grinding and polishing of surfaces, which is made possible by built-in force sensors. The main benefits are:
- Accuracy and repeatability.
Ideal for tasks that require gentle pressure, such as removing bumps or smoothing surfaces. - Consistent work quality.
Cobots can perform the same operations for a long time without losing quality, which is difficult to achieve with manual operations. - Safety.
Operators are relieved from performing monotonous and potentially dangerous manual work.
Bonding and dispensing
Doosan cobots can precisely dispense adhesives or other substances, ensuring a consistent amount of applied material in the bonding and joining processes of components. With advanced programming features, cobots can:
- Precisely control the amount of glue applied.
Cobots guarantee accurate and even application of glue to the surface, which is key to ensuring high quality joints. - Customize the application according to product requirements.
Regardless of the shape and size of the components, the cobot can precisely apply glue in the right places according to the programmed path. - Optimize the bonding process.
Process automation speeds up production and minimizes waste with accurate dispensing control.
Air cleaning
Doosan Cobots can be equipped with tools for cleaning surfaces with compressed air, which is especially suitable for delicate processes where dust, chips or other external contaminants need to be removed. The main advantages of this solution are:
- Effective dirt removal.
Cobots can work with great precision, directing the airflow exactly where it is needed, eliminating unnecessary materials from the surface of products. - Minimizing the risk of damage.
By precisely controlling the force and direction of the air stream, the cobots provide gentle cleaning, which is important for sensitive materials. - Automation of repetitive tasks.
Cobots can perform cleaning processes continuously and repetitively, reducing the need to involve humans in monotonous and time-consuming activities.
Quality control
Doosan cobots are the perfect tool for quality control tasks, both visual and mechanical. By integrating with vision systems and sensors, cobots can:
- Inspect products for external defects.
Cobots can quickly and accurately detect surface defects such as scratches, dents or improper finishes. - Verify the quality of assembly.
Verify the correct assembly of components, which is especially important in industries where high accuracy is crucial, such as automotive and electronics. - Detect internal defects.
Using advanced sensors, cobots can test the structural integrity of components, identifying internal cracks or other manufacturing defects.
Contact us to learn how Doosan cobots can improve your manufacturing processes.
Doosan Cobots are versatile and flexible, allowing them to automate a variety of production tasks - from gluing and dispensing to air cleaning and quality control.
Each of these applications is optimized for precision, repeatability and safety, providing better production results and significant savings in time and resources.
Types and Technical Specifications of cobots
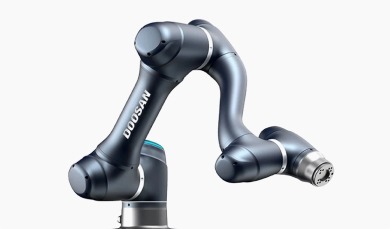
Doosan – A series
Versatile and economical cobot, ideal for dynamic tasks.
Lifting capacity:
up to 9 kg
Range:
to 1,200 mm
Repeatability:
0.1 mm
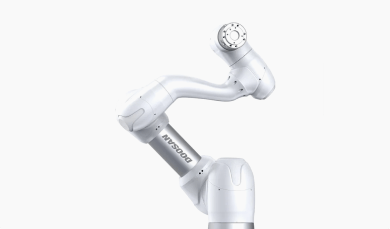
Doosan – M series
Premium cobot with 6 torque sensors, maximum precision and safety.
Lifting capacity:
up to 9 kg
Range:
to 1,200 mm
Repeatability:
0.1 mm
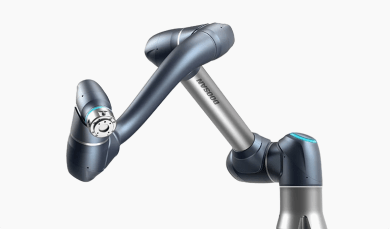
Doosan – H Series
The most powerful cobot, lifting capacity of 25 kg, precision and safety.
Lifting capacity:
up to 9 kg
Range:
to 1,200 mm
Repeatability:
0.1 mm
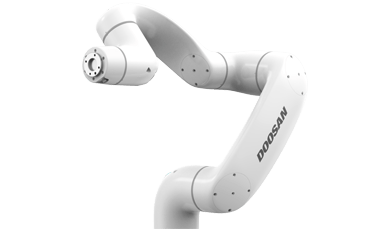
Doosan – E Series
Cobot for food industry, NSF, IP66, maximum performance.
Lifting capacity:
up to 9 kg
Range:
to 1,200 mm
Repeatability:
0.1 mm
Step by Step
Implementing a cobot in a company may seem like a complicated process, but following well-defined steps can ensure a smooth and efficient launch. The Doosan Robotics cobot implementation process, from purchase to launch, looks like this.
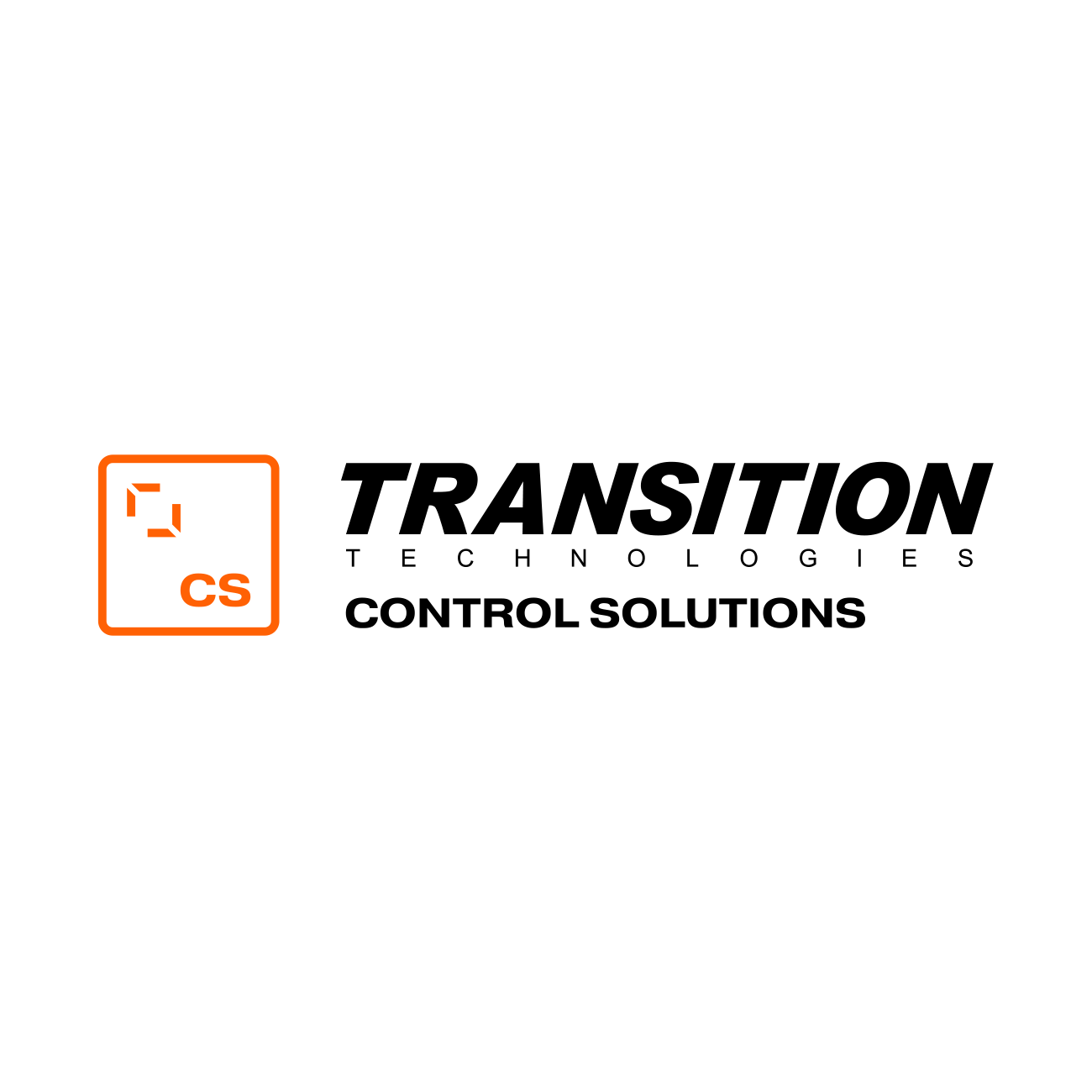
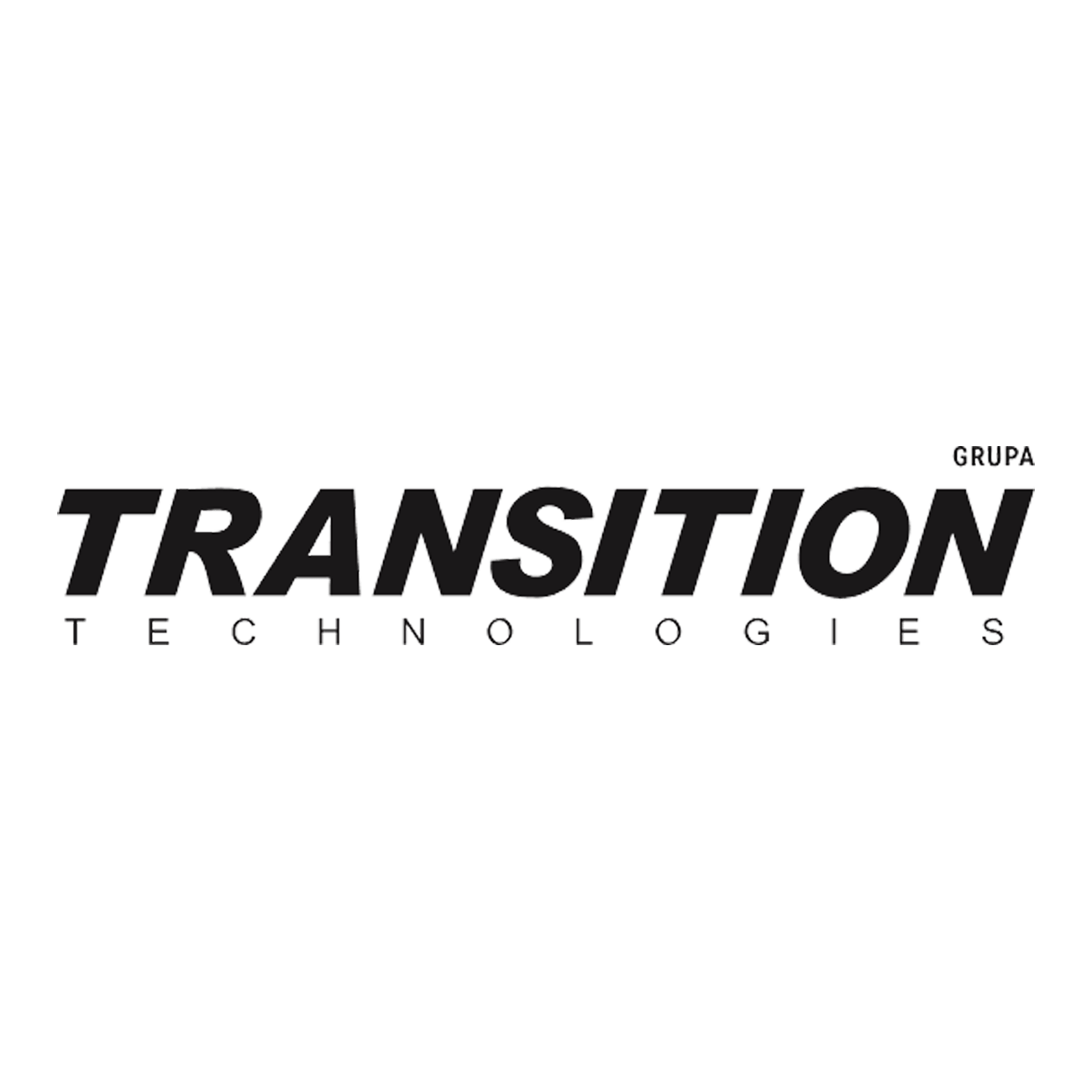
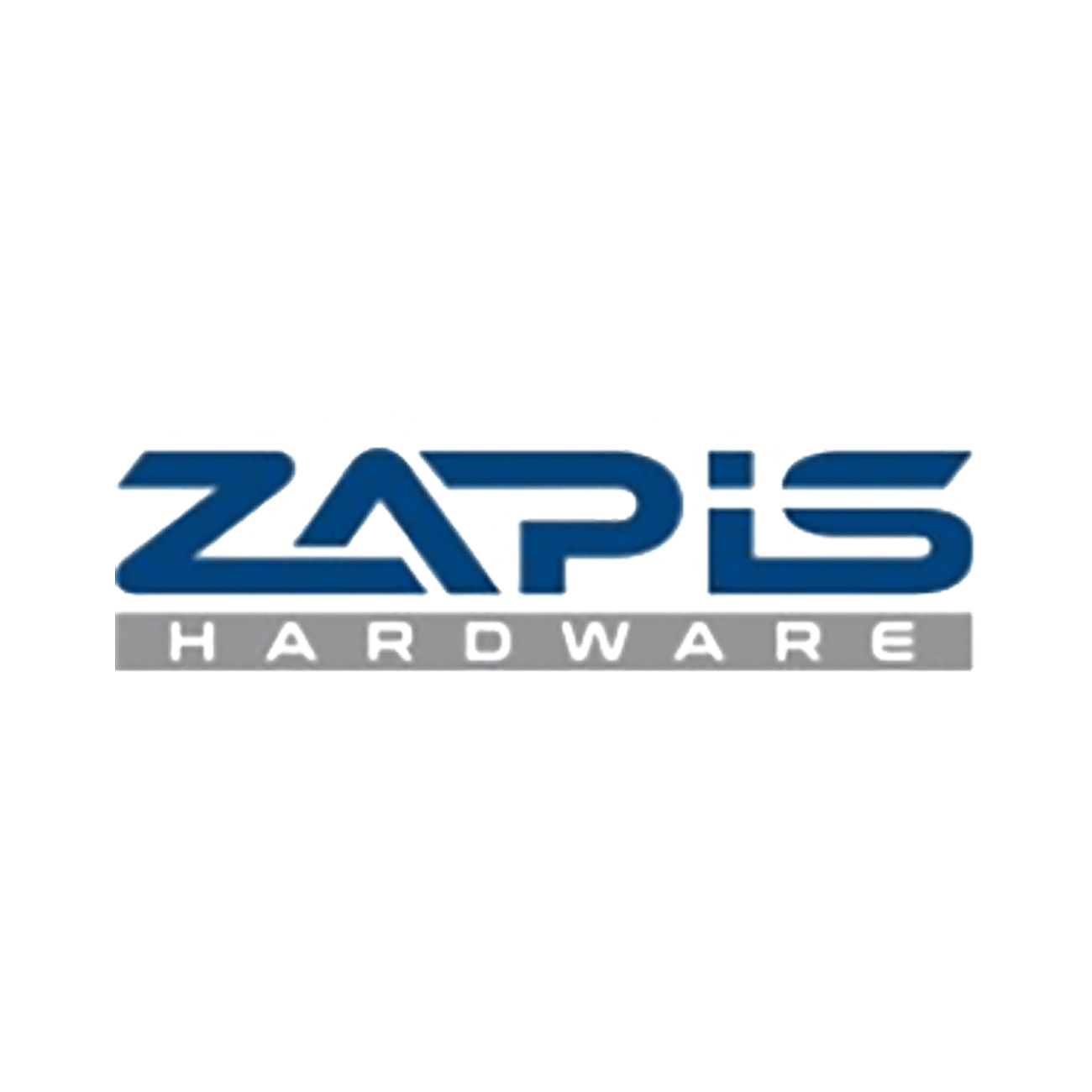
Competitive Advantage
We are part of the renowned Transition Technologies Group, which has been creating the future of industrial technology since 1991. The group includes 21 companies, employs more than 2,280 specialists and operates from 27 offices around the world, operating with 100% Polish capital. Our mission is to provide innovative technology solutions that drive global industry growth.
- Innovation: We constantly invest in the latest technologies to keep our solutions at the forefront of innovation.
- Experience: More than three decades in the industrial technology market provide us with the knowledge and skills needed for the most demanding projects.
- Quality: We are ISO 9001:2015, ISO 27001:2013 and ISO 45001:2018 certified, confirming our commitment to the highest standards of quality and safety.
When you choose our solutions, you are investing in the future of your business – a future that is innovative, efficient and sustainable.
We work with the best:


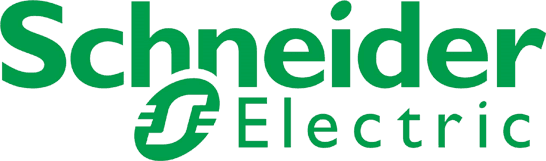
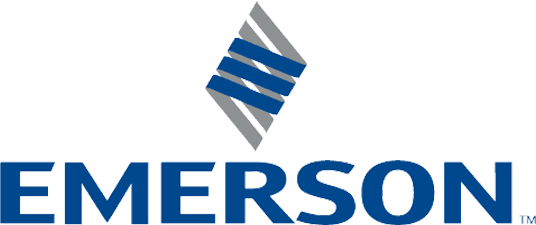

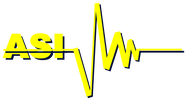
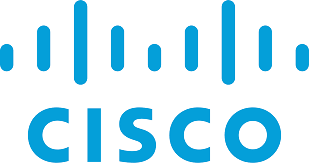
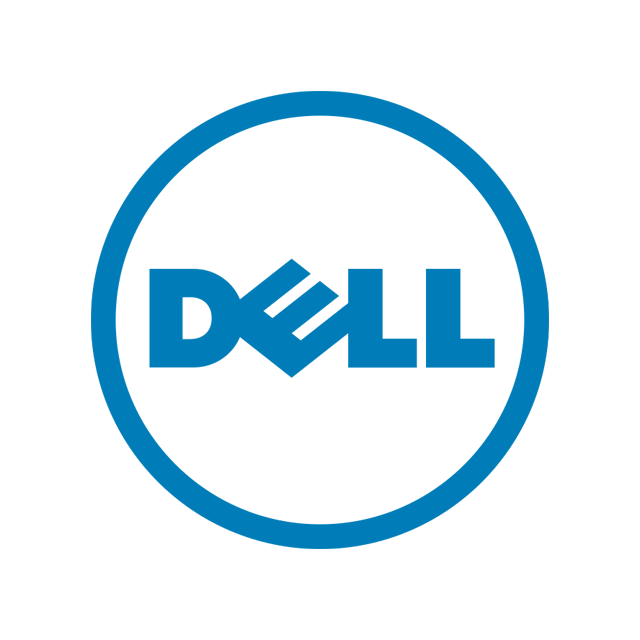
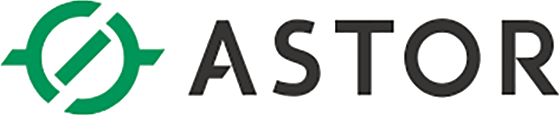
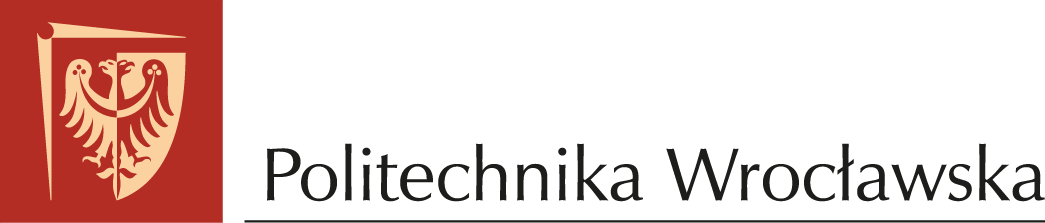
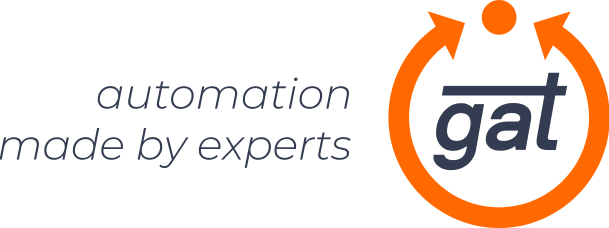
Opinions of Our Customers
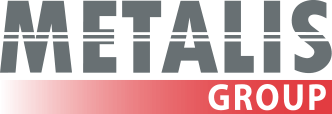
”From the very beginning of our cooperation, Transition Technologies-Control Solutions has made itself known as a reliable partner. What set them apart was their creative approach at the bidding stage. We were presented with several proposals for solutions based on which we could choose a target direction.</p>
Adam BombaProcess Manager
<p>During implementation, on the other hand, they acted with determination, solving successive problems that arose. Faced with the fact that the project was implemented in a difficult market environment, we often had to work together and develop remedies, often through compromise. Also, during the operation of the site, they reacted constructively and quickly to faults as they appeared.</p>
<p>TT-CS has proven itself as a trusted partner in challenging projects. We positively look forward to working together on future mechanical engineering projects.
Our team
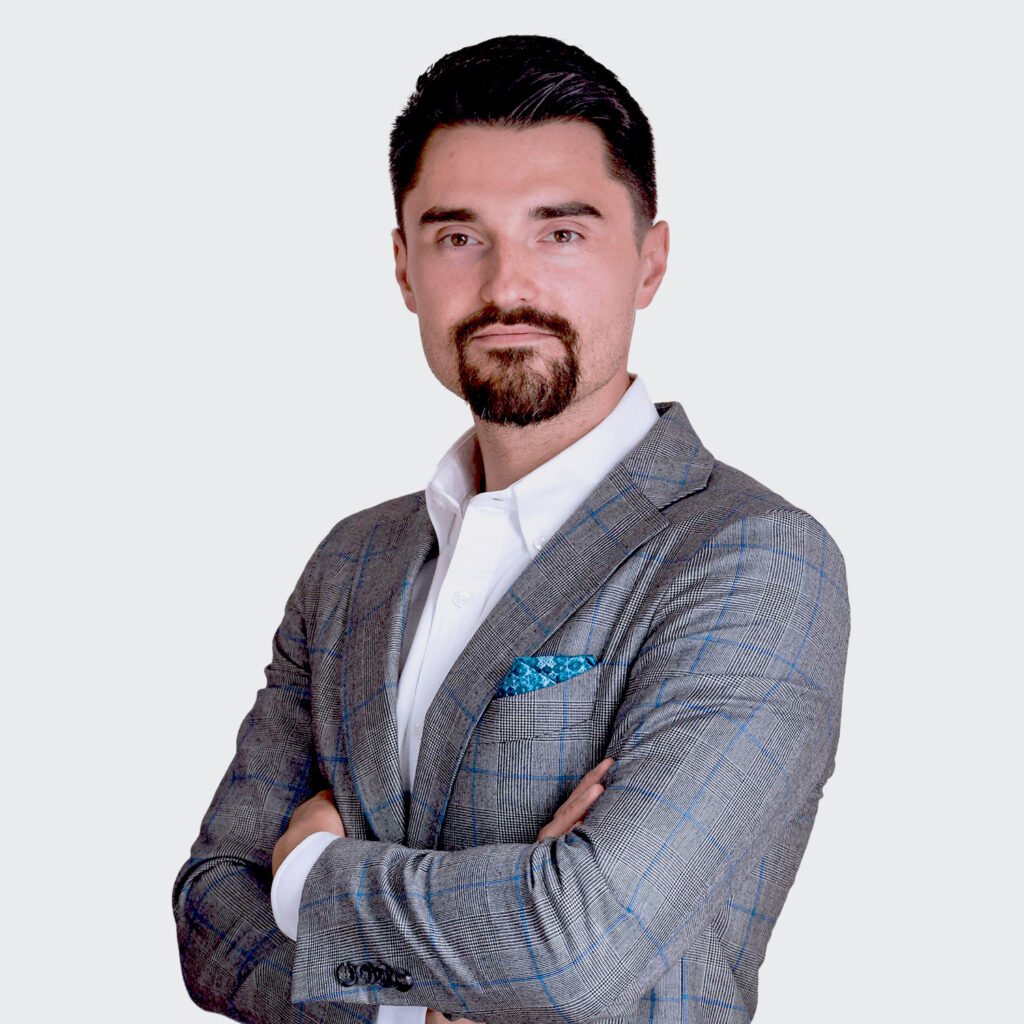
Director of the robotics area at Transition Technologies-Control Solutions. A mechanical engineer by training and passion.
He has many years of experience in manufacturing process automation and project management. With the company for 3 years, he is currently in charge of business development of the robotics department and coordinating its work.
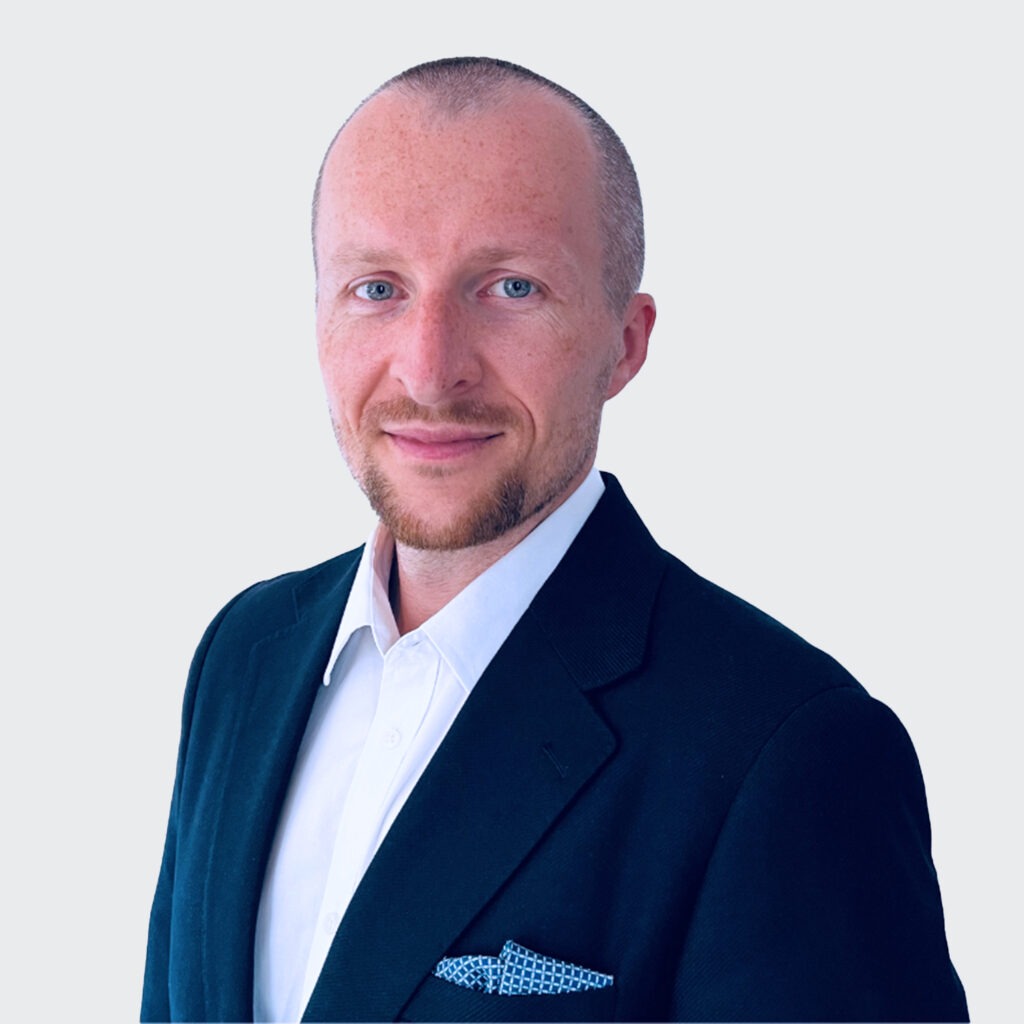
Project coordinator at Transition Technologies-Control Solutions. A mechanical engineer by training with a DIY vein.
He has extensive experience in process management. Performs tasks in automation and robotics projects.
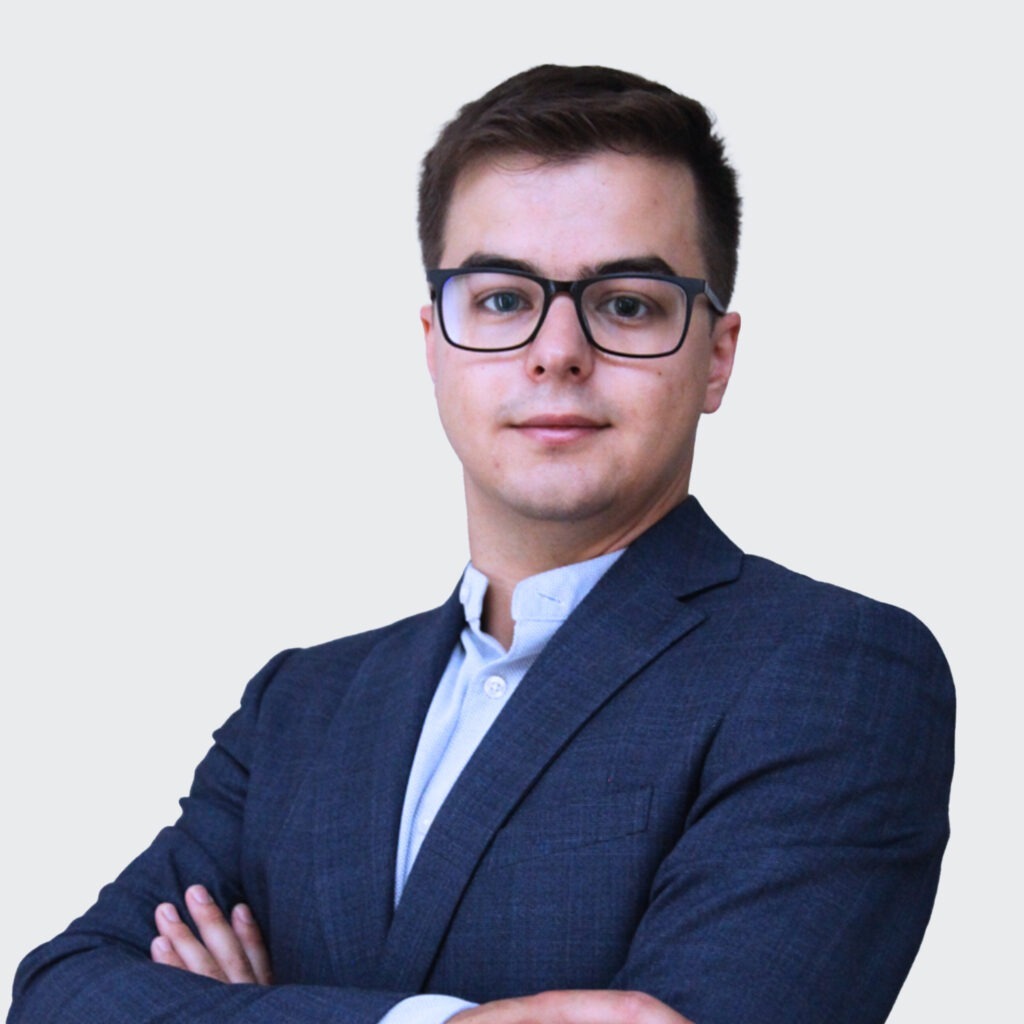
Automation engineer at Transition Technologies-Control Solutions, a graduate of the Faculty of Mechanical Engineering at Wroclaw University of Technology.
He has been professionally involved in industrial automation for 5 years. Performs tasks in robotics and mechanical engineering projects.
We Are Here to Help
Are you interested in our offer?
Write to us for a personalized consultation.
- Individual counseling
- Tailored solutions
- Quick implementation
- Experts with experience
Fill out the form and get a free consultation
Questions
and answers
In the FAQ section, you will find answers to key questions about our services and processes, based on knowledge and experience. Our goal is to dispel doubts and provide clear information.
What are cobots and how do they differ from traditional industrial robots?
Cobots (collaborative robots) are state-of-the-art robots designed to work safely in close proximity to humans, without the need for enclosure or protective cages.
Unlike traditional industrial robots, which must be separated from workers, cobots are equipped with advanced force sensors and collision detection systems, allowing them to react safely to their surroundings.
In addition, cobots tend to be easier to program and more versatile, so they can be quickly adapted to new tasks.
What are the benefits of implementing Doosan cobots in manufacturing processes?
Doosan Cobots offer a wide range of benefits that can significantly improve production efficiency:
-Flexibility: Cobots are easily programmable and can be quickly adapted to different tasks, allowing them to respond dynamically to changing production needs.
-Safety: With advanced safety features, Doosan cobots can work directly next to people, reducing the risk of accidents.
-Cost Reduction: Automation of repetitive tasks reduces human labor costs and increases productivity while minimizing the risk of errors.
-Increased productivity: Cobots can operate without interruption, allowing for more efficient use of production time, while increasing the accuracy and repeatability of operations.
What is the process of integrating Doosan cobots into an existing production line?
Integrating Doosan cobots into existing production systems is a relatively quick and simple process, thanks to the flexibility of these devices and their compatibility with a variety of communication standards (such as Profinet, Ethernet/IP, Modbus). The integration process typically includes:
-Production process analysis: First, a detailed process analysis is conducted to determine where cobots can bring the greatest benefit.
-Cobot model selection: Based on the requirements for payload, reach and precision, a suitable cobot model is selected.
-Installation and programming: once a cobot has been selected and delivered, installation and adaptation to existing production systems is carried out. Programming is done through an intuitive interface, which reduces implementation time.
-Testing and optimization: the final step is to test and optimize the process to ensure full functionality.
What are the typical applications of Doosan cobots in various industries?
Doosan Cobots are used in a wide range of industries and manufacturing processes. They are most often used in tasks such as:
-Palletization and depalletization: automate the processes of stacking products on pallets and unpacking them.
-Welding: Precision welding of parts using defined paths, with high repeatability.
-Mounting and screwing: Automated joining of components and screwing of parts in various production processes.
-Quality inspection: Visual and mechanical inspection of products, detection of defects, and inspection of correct assembly.
-Pick& Place: Moving and positioning products, often in conjunction with vision systems.
-Gluing and dispensing: Accurately apply adhesives or other substances according to programmed paths.
Is it safe for workers to deploy Doosan cobots?
Yes, Doosan cobots are designed for maximum safety. They are equipped with advanced force sensors that allow the robot to detect collisions immediately and stop automatically. Doosan cobots meet ISO 10218 and ISO/TS 15066 safety standards, which regulate the safe interaction of robots with humans. In addition, the cobots offer programmable safety features such as speed and force torque limitation, further enhancing safety.
What are the costs and time to implement Doosan cobots in a company?
The cost of implementing cobots depends on a number of factors, such as the number of robots, the specification of the task, the complexity of integration with existing systems, and the need to purchase additional tools, such as grippers or vision systems. As a rule, the implementation of cobots is more cost-effective than traditional industrial robots, as it requires less investment in installation and integration.
Deployment time also depends on the complexity of the application. For simpler processes, cobots can be up and running in a matter of hours, while more complex jobs may require days or weeks for full integration and testing.