When assembling and servicing industrial machinery, we face such problems and challenges as:
Installation and service
We perform service inspections of machines we have manufactured, as well as equipment from other manufacturers at the request of partners.
Find out how we can support your business
Problems and challenges
Maintaining a high level of work safety
Mechanisms equipped with servo or pneumatic actuators generate the risk of crushing hands. The presence of electricity, compressed air or hydraulic oil are other risks that should be approached with due caution.
A race against time
Each stage in the project has a specific time frame. Assembly of the machine must take place on time so that programmers and roboticists can begin their scope of work in a timely manner.
Ensuring the highest quality
Despite the high pace of work, we cannot afford to reduce the quality of our work. We always maintain a professional approach and uphold our work standards.
Step by Step
Deeply rooted in our DNA is a culture of continuous improvement reflected in the process of delivering value to our customers. We use the PDCA methodology in practice. Plan, Execute, Check and Revise – these are the stages into which we have written typical milestones in our projects.
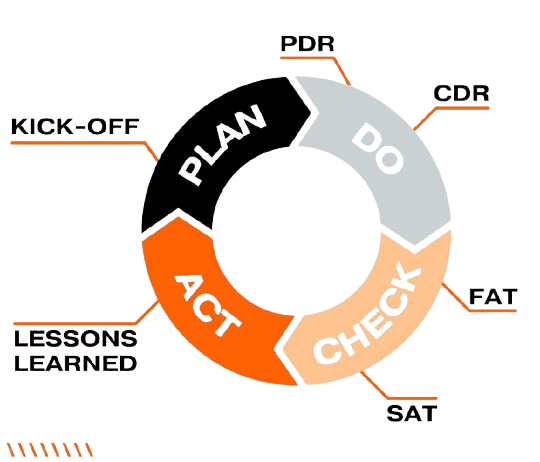
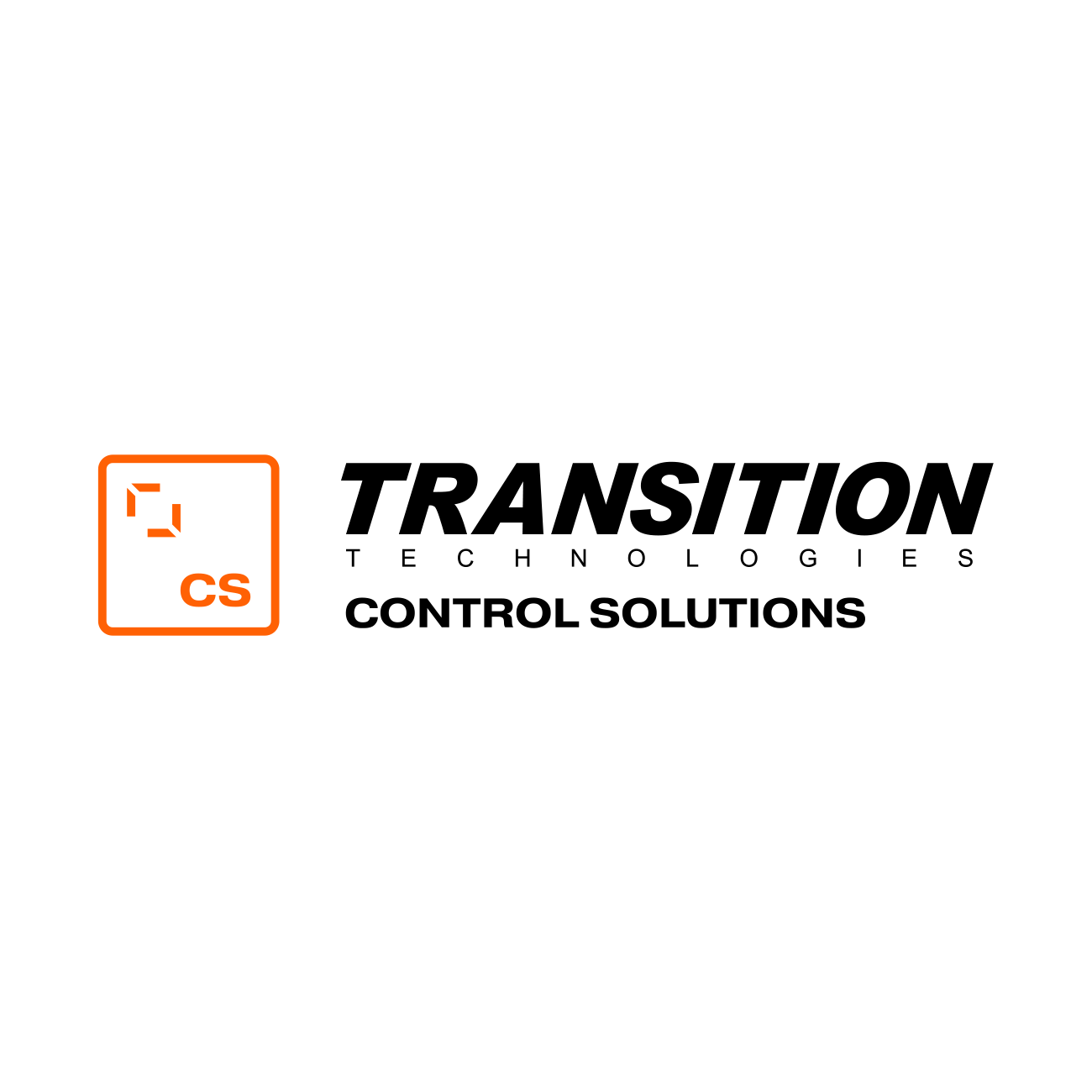
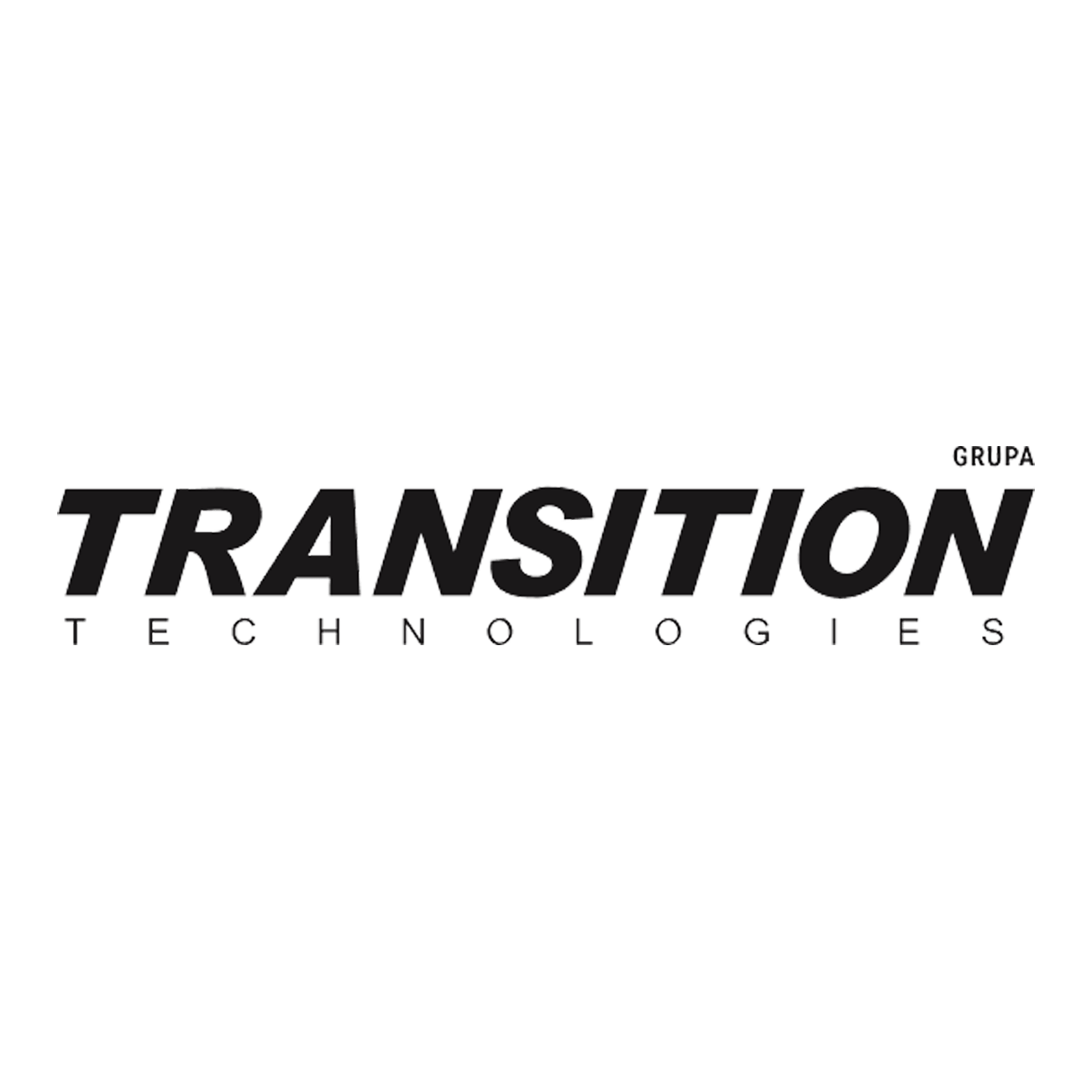
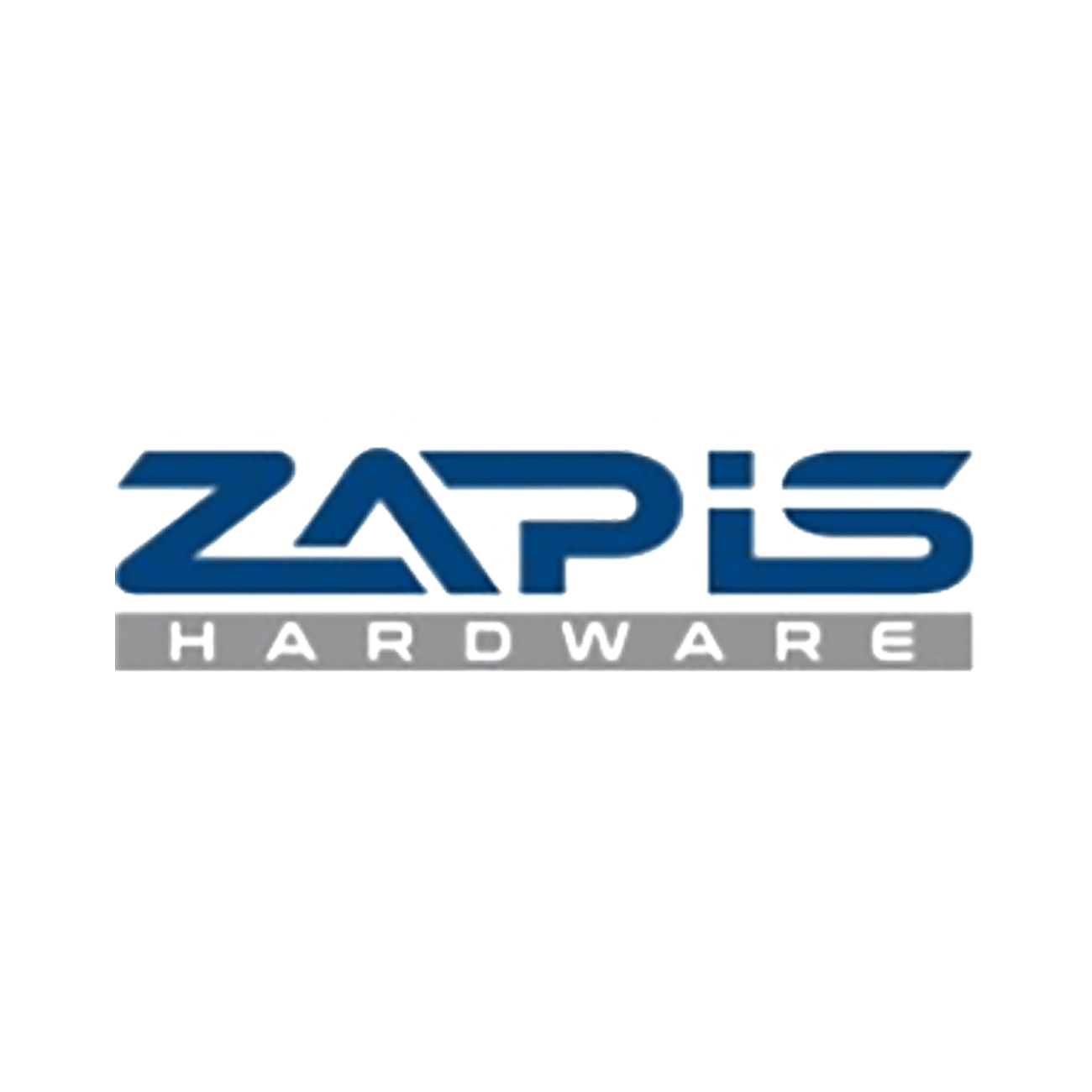
Competitive Advantage
We are part of the renowned Transition Technologies Group, which has been creating the future of industrial technology since 1991. The group includes 21 companies, employs more than 2,280 specialists and operates from 27 offices around the world, operating with 100% Polish capital. Our mission is to provide innovative technology solutions that drive global industry growth.
- Innovation: We constantly invest in the latest technologies to keep our solutions at the forefront of innovation.
- Experience: More than three decades in the industrial technology market provide us with the knowledge and skills needed for the most demanding projects.
- Quality: We are ISO 9001:2015, ISO 27001:2013 and ISO 45001:2018 certified, confirming our commitment to the highest standards of quality and safety.
When you choose our solutions, you are investing in the future of your business – a future that is innovative, efficient and sustainable.
We work with the best:


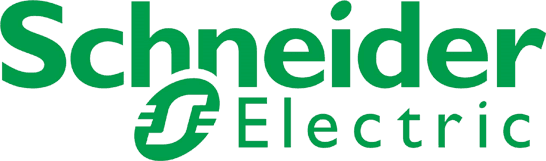
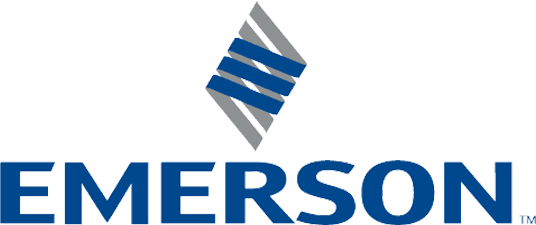

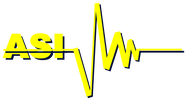
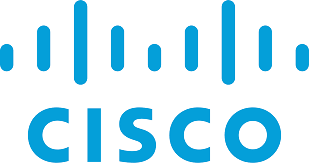
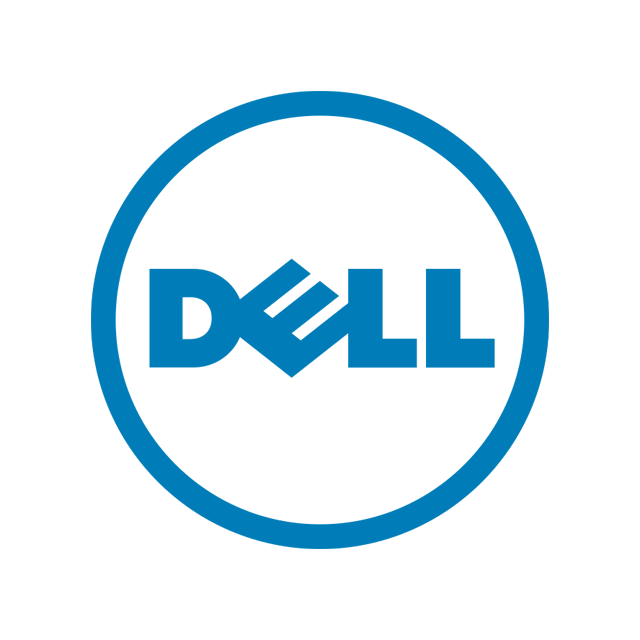
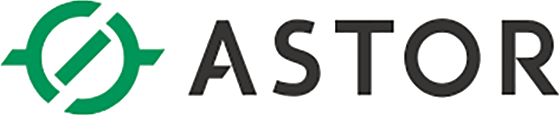
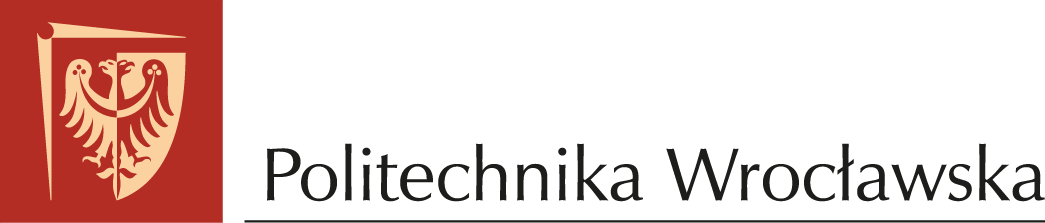
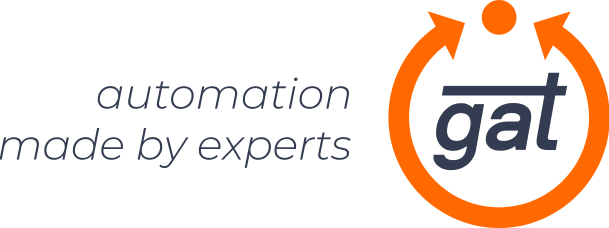
Opinions of Our Customers
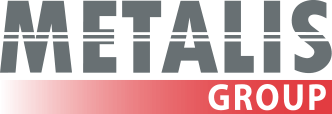
”From the very beginning of our cooperation, Transition Technologies-Control Solutions has made itself known as a reliable partner. What set them apart was their creative approach at the bidding stage. We were presented with several proposals for solutions based on which we could choose a target direction.</p>
Adam BombaProcess Manager
<p>During implementation, on the other hand, they acted with determination, solving successive problems that arose. Faced with the fact that the project was implemented in a difficult market environment, we often had to work together and develop remedies, often through compromise. Also, during the operation of the site, they reacted constructively and quickly to faults as they appeared.</p>
<p>TT-CS has proven itself as a trusted partner in challenging projects. We positively look forward to working together on future mechanical engineering projects.
Our team
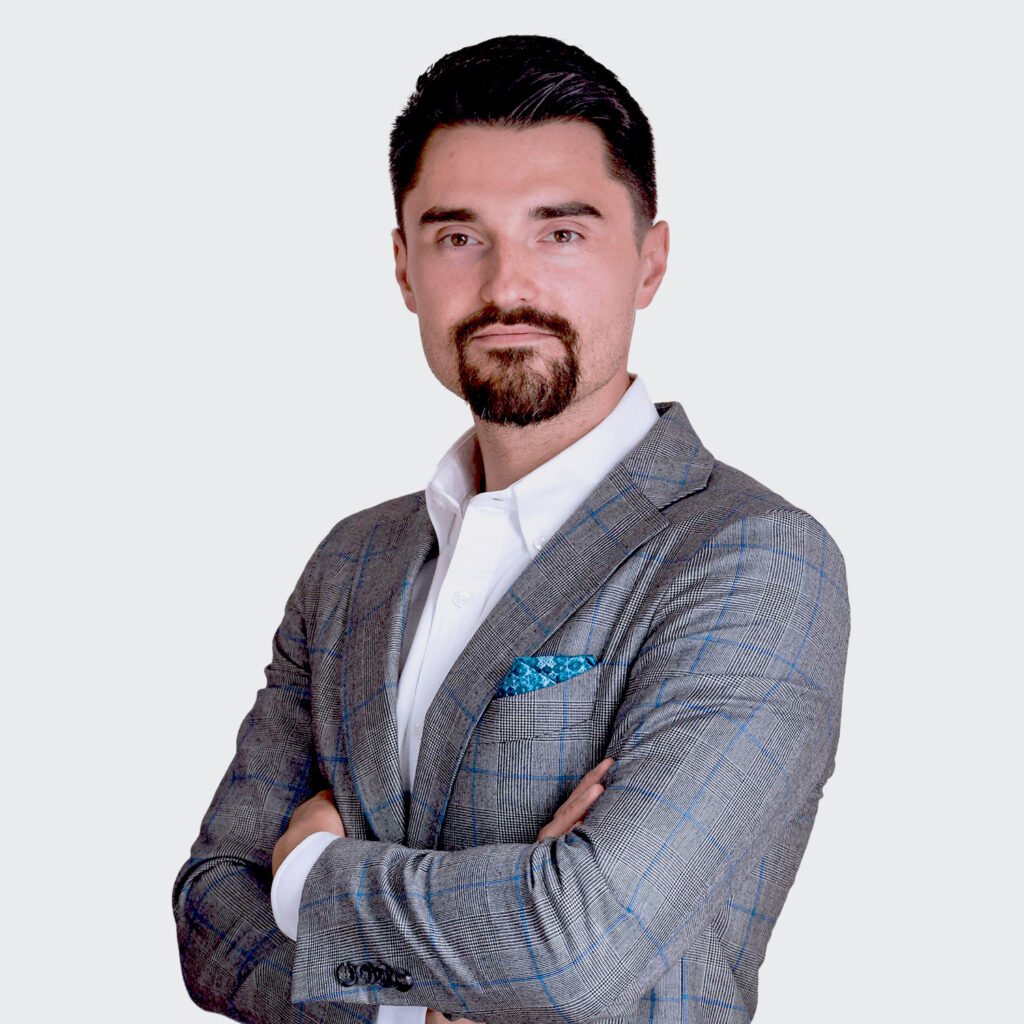
Director of the robotics area at Transition Technologies-Control Solutions. A mechanical engineer by training and passion.
He has many years of experience in manufacturing process automation and project management. With the company for 3 years, he is currently in charge of business development of the robotics department and coordinating its work.
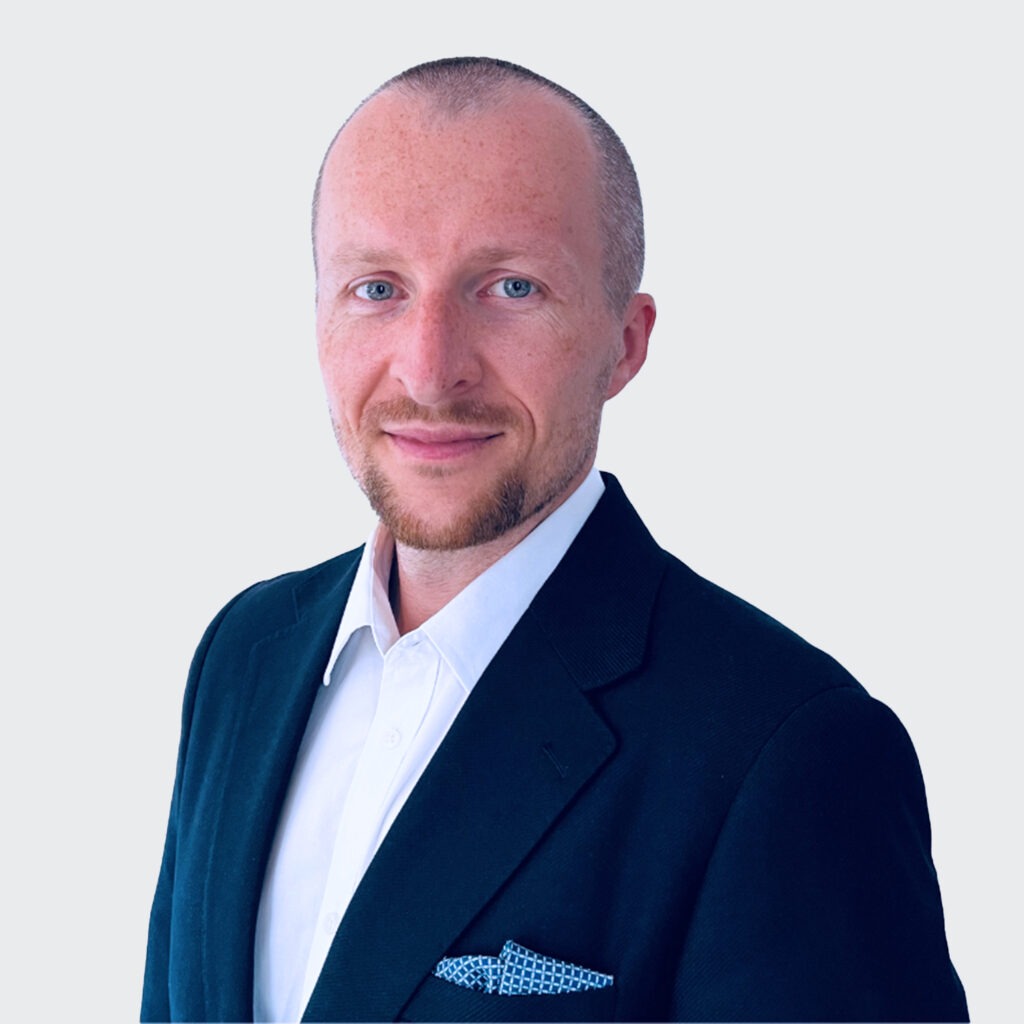
Project coordinator at Transition Technologies-Control Solutions. A mechanical engineer by training with a DIY vein.
He has extensive experience in process management. Performs tasks in automation and robotics projects.
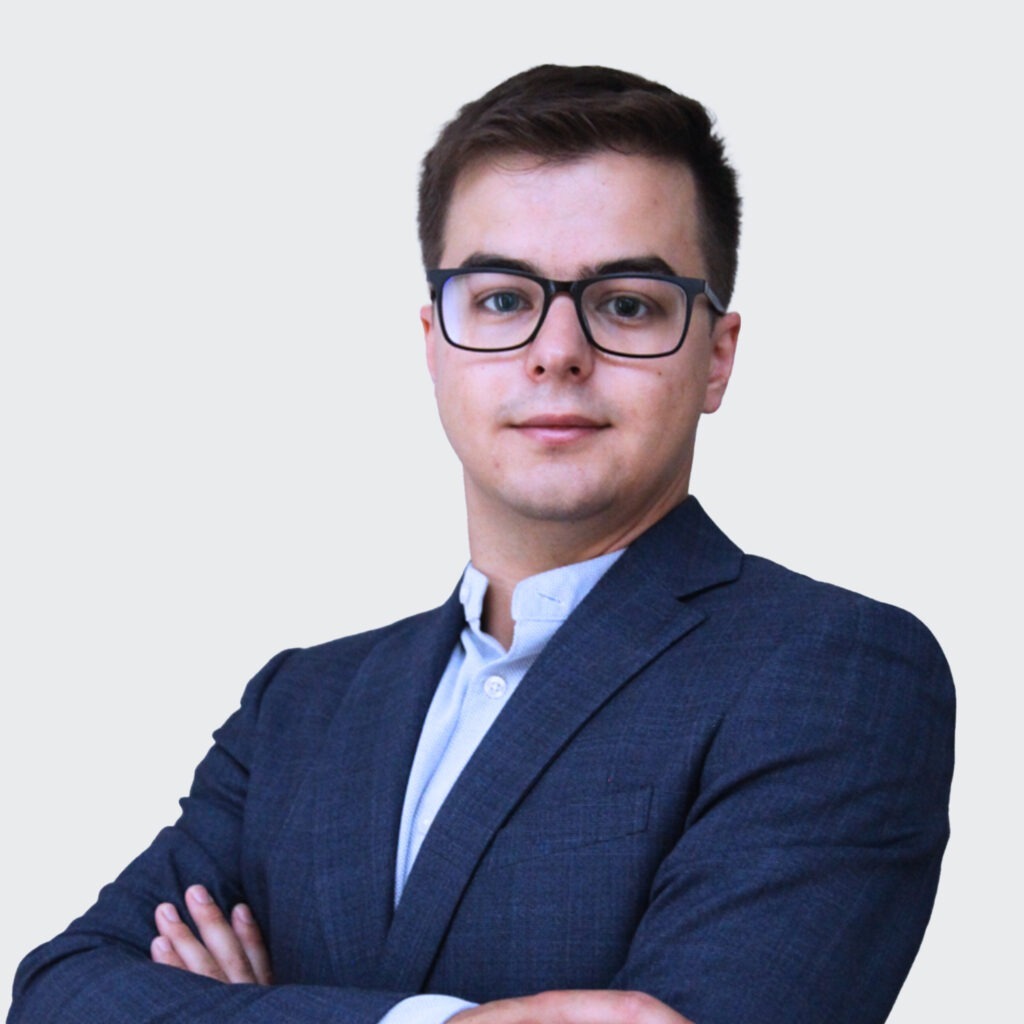
Automation engineer at Transition Technologies-Control Solutions, a graduate of the Faculty of Mechanical Engineering at Wroclaw University of Technology.
He has been professionally involved in industrial automation for 5 years. Performs tasks in robotics and mechanical engineering projects.
We Are Here to Help
Are you interested in our offer?
Write to us for a personalized consultation.
- Individual counseling
- Tailored solutions
- Quick implementation
- Experts with experience